Introducción
Todos aquellos pasivos ambientales y residuos mineros consistentes en infraestructura y en desuso como: refinrías, fundiciones abandonadas, despojos de minas ya cerradas, así como los desechos de las minas en actual explotación, se han diseminado en territorios y otros ecosistemas vivos, cubriéndolos con mini-escorias “rebaba” y hierro en polvo, los cuales, con el transcurso del tiempo se han apilado y sedimentado conformando superficies de territorios altamente contaminados. A la fecha, luego de cientos de años, se ha convertido en una alternativa de espacio geográfico para la expansión de la mancha urbana, a estos cúmulos de relaves se les llama “lameros” y “terreros”. Con la presencia de las lluvias se forma suelo húmedo y es entonces cuando los metales pesados se combinan en otros elementos y forman cloruros y sulfatos que son los directos agentes corrosivos que deterioran las estructuras de concreto que conforman la estructura de las viviendas afectadas. Una forma de combatirlos es re-utilizarlos en contra de su mismo efecto contaminante, mediante su inclusión como nuevos materiales de construcción, que sean amigables con el medioambiente. De esta manera, en un futuro próximo se podrán producir agregados artificiales a partir de las escorias siderúrgicas procedentes de los mismos residuos de minas, próximos a las poblaciones afectadas, reutilizándose el residuo en beneficio tanto del medio ambiente como de la salud pública de los pobladores.
Desarrollo
El diseño de la pasta cementicia mejorada (Patente No 000181-2018/ INDECOPI-Perú) (Vera, 2018), consiste en un mortero de pega o junteo parcialmente compuesto por agregados artificiales, destinado a utilizarse en las obras de albañilería. El desarrollo experimental para su obtención, se divide en dos etapas, la primera, en diseñar un mortero mejorado con 4 posibles variantes (Figura 1) en función de combinar hierro con zeolita adicionándolos al mortero convencional y la segunda, en perfeccionar la mezcla con base en un estudio basado en procesos de catálisis heterogénea, con el fin de eliminar el poder contaminante del hierro, accionándolo sobre la “zeolita” como sustancia de soporte. La pasta en mención, incluye como insumo al hierro en polvo, específicamente el que proviene de los residuos minero-siderúrgicos, y la zeolita, que es un aditivo mineral del tipo clinoptilolita-heulandita, el cual sustituye el clinquer que forma parte de los cementos convencionales. Con ello, se reduce el consumo de energías no renovables como el “combustible con base en petróleo”, evitándose la emanación de gases contaminantes expulsados a la atmosfera. En este trabajo se desarrollarán los alcances encontrados en la primera etapa de la investigación.
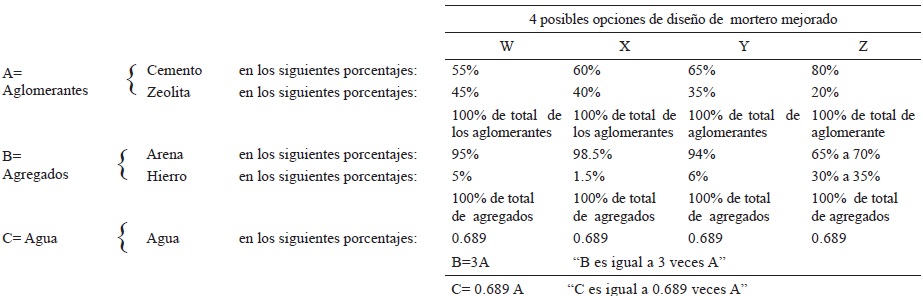
Fuente: Elaboración propia según normas ASTM-270
Figura 1 Proporciones de diversos propuestos para los morteros mejorados
La presencia de residuos tóxicos esparcidos tanto en el medio terrestre como en la atmósfera, han contaminado los hábitats construidos produciendo daño irreversible en los ecosistemas vivos que coexisten con el poblador de regiones mineras. En las construcciones existentes, tanto en fachadas exteriores como interiores, las paredes presentan deformaciones, manchas de eflorescencias y un acelerado deterioro tanto del concreto de revestimiento en paredes, como del mortero de pega.
Objetivo general
Estudiar y evaluar si la incorporación del hierro, producto residual de la post-minería, al ser incluido como insumo alternativo en sustitución parcial de la arena, incrementa los niveles de resistencia mecánica a la compresión simple dentro de la pasta cementicia de los morteros mejorados de pega obtenidos de “cemento, arena, zeolita y agua”, de acuerdo con las Normas ASTM C-270 y ASTM C-780. De verificase su eficiencia, estaríamos encontrado nuevas cualidades a las ventajas ya conocidas de los compuestos cementicios que utilizaban zeolita, cemento, arena y agua.
Antecedentes o estado de la técnica
Mezcla de hormigón obtenida de arena de relaves de hierro (Hezhao et al., 2010). Un concreto obtenido de una mezcla de arena de presas de jale mineros, caracterizado por la siguiente composición: cemento de 16 a 20% de la mezcla, grava de 22 a 27%, arena de colas de mineral de hierro de 45 a 48% de agua, rangos de 5.5 a 6.5% a 7.3 a 8.1%, y policarboxilato superplastificante de 0.2 a 0.3%. La desventaja de la propuesta radica en que los productos se obtienen del hierro en cantidades muy elevadas, de 48%, por lo que necesita añadir bastante cantidad de agua, es por ello que recurren a los policarboxilatos para reducir la proporción de agua. El hecho de que presenten una granulometría más fina, hace suponer que su contenido de material fino es mayor, consecuentemente su área superficial específica es mayor, y se tendrá un mayor requerimiento de agua para alcanzar consistencia, fluidez y viscosidad.
Evaluación térmica de morteros elaborados con zeolita como porcentaje de sustitución de aglomerante. Los investigadores Andrada et al. (2012) de la Facultad Regional Córdoba, Universidad Tecnológica Nacional de la República de Argentina publicaron el artículo en referencia. En este trabajo se reemplaza al cemento con zeolita por las ventajas económicas y sustentables al no demandar gasto energético y cuidar el medio ambiente, además, por las propiedades térmicas de la zeolita.
Utilización de las presas de relaves de hierro como agregados finos en concretos de alta resistencia. Los investigadores Sujing et al. (2014) publicaron que directamente se sustituye 40% del total de los agregados finos por el hierro en polvo, obteniéndose resultados similares al comportamiento de la arena natural.
Justificación de la elección del compuesto cementicio
Se pretende indagar cuáles son los procedimientos técnicos más adecuados para mejorar las propiedades mecánicas de resistencia y durabilidad de los actuales morteros de pega, debido a que exteriormente, presentan decoloración, eflorescencia y manchas de óxido, producto del uso de agregados contaminados. El mortero al dañarse ya no permite un acabado correcto, además expone a los usuarios al contacto con agentes contaminantes, plomo, zinc y hierro. La denominación técnica de mortero de junteo según la Norma Mexicana es “mortero para mampostería sin refuerzo”, y pueden ser del tipo M, S o N (Gutiérrez, 2010) norma ASTM C-270 y ASTM C-780 (Tablas 1 y 2). En este estudio se propone un mortero-prototipo sencillo y ecológico, mismo que se encuentra en desarrollo, la mayor parte de los resultados del ensayo de resistencia mecánica superan el valor mínimo que establece la Norma de 5.2MPa, pero no sobrepasan los 18.31 MPa, como los alcanzados por los morteros de las Muestras Patrón, estos valores se encuentran comprendidos entre los rangos del “Mortero tipo N” y “Mortero del tipo S”.
Tabla 1 Tipos de mortero de pega, según la NSR/98 “Norma colombiana de diseño y construcción sismoresistente
Proporciones de mortero por volumen | |||
---|---|---|---|
Tipo de mortero | Partes de cemento por volumen | R’m(Mpa) | Resistencia en kg-f/cm2 |
M | 1 | 17.5 | 175 Kg/cm2 |
S | 1 | 12.5 | 125 Kg/cm2 |
N | 1 | 7.5 | 7.5 Kg/cm2 |
Tabla 2 Clasificación de los morteros de pega para mampostería simple según resistencia a la compresión a 28 días y según dosificación
Tipo de | Resistencia a la Compresión | Cemento | Cemento | Cal | OBSERVACIONES | ||
---|---|---|---|---|---|---|---|
Mortero | Mpa | Kg-f/cm2 | P.S.I | Portland | Albañilería | ||
M | 17.2 | 175 | 2500 | 1 | 1 | 0.25 | En esta investigación no se incluye la “cal” como aglomerante |
S | 12.4 | 126 | 1800 | 0.5 A 1 | 1 | 0.25 a 0.50 | |
N | 5.2 | 53 | 750 | 1 | 1 | 0.50 a 1.25 | |
O | 2.4 | 25 | 350 | 1 | 1 | 1.25 a 2.50 | |
K | 0.5 | 5 | 75 | 1 | 2.50 a 4.00 |
El mortero para mampostería debe ser M, S, N
Fuente: Universidad Nacional de Colombia-Biblioteca Digital UCol.www.bdigital.unal.edu.co/6167/17/9589322824_Parte5.pdf
Los insumos de los que está elaborados son cemento portland compuesto, zeolita clinoptilolita, arena y hierro en polvo. Luego de revisar los resultados que se encontraron en el actual estado de la técnica (Parra, 2011) se realizó la experimentación reemplazando parcialmente al cemento por zeolita en porcentajes diversos comprendidos entre 20 y 45% en distintos ensayos, esto le permitió obtener resultados aceptables en los valores de resistencia mecánica (Figura 2). La zeolita clinoptilolita es una puzolana natural, cumple con los parámetros de la norma ASTM C 618-01, esta última es la que clasifica a la zeolita como una puzolana tipo N dentro de los grupos N, F y C. En cuanto al hierro, este insumo por razones experimentales se adquirió como hierro reducido, presentó una densidad elevada de 6.78gr/cm2, y un tamaño de partícula de 75 µm (malla 200). Como se mencionó, los morteros realizados en esta investigación presentaron resistencias coincidentes con la Norma, obteniéndose valores, que van desde los morteros tipo N (Rivera, 2015), hasta valores que sobrepasan el tipo S. Para las proporciones en porcentaje diversas, se consideraron 4 posibles opciones de diseño de mortero mejorado y una relación agua/cemento de 0.68 promedio. Para una mejor comprensión, se agruparon zeolita y cemento portland, bajo la denominación de aglomerantes y se agruparon bajo la denominación de agregados, la arena y el hierro (Figura 1). Al interior de cada subgrupo se realizaron varias subcombinaciones de zeolita y cemento para el primero, y de hierro y arena para el segundo, de modo tal que la suma de cada par no alterara la suma total de la proporción de aglomerante inicial ni del grupo de agregados inicial (Figura 1). El rango de variaciones entre las sub-combinaciones de zeolita y cemento al interior de material aglomerante se encuentra entre el rango de 20 a 45%, según la norma ASTM C595, mientras que para el material agregado, las subcombinaciones entre arena y hierro oscilan entre 1.5 y 30%, (Figura 1), estas variaciones pueden resistir mejor un posible ataque químico por corrosión y mejores propiedades de durabilidad y resistencia mecánica, la zeolita es un mineral que tiene alta resistencia a sulfatos, y el hierro en polvo (Umara et al., 2016), sustituyente de la arena, eleva las cualidades de durabilidad en el tiempo. Al final del experimento, estos morteros deben presentar las siguientes características: Fraguado, Fluencia, Resistencia y Durabilidad. La zeolita también se molió para cumplir lo que prescriben las Normas ASTM C-430 y ASTM C-618.
Discusión y análisis de resultados
Las muestras de control se componen de una parte de Cemento Portland Compuesto, 3 partes de arena y agua necesaria hasta alcanzar una fluidez del orden de 110% ´+/-5., se hicieron 3 muestras en total. Todas las muestras se realizaron con base en el molde normalizado tipo cilíndrico D= 5cm x H= 10cm según las normas ASTM C470 / C470M -15, los colados se hicieron en 3 etapas hasta obtener un total de 16 especímenes cilíndricos entre los meses de abril-julio del año 2016, del total, 2 se reservaron para posteriores estudios de microscopia de barrido o análisis SEM.
Materiales y métodos
En este artículo se presentan los resultados de los siguientes estudios: prueba de resistencia mecánica a la compresión y prueba de revenimiento o asentamiento.
Dosificación y revenimiento
A raíz de la existencia de una gran cantidad de métodos empíricos de diseño de mezclas para obtener concretos y morteros con características específicas, los cuales siempre requieren pruebas de laboratorio para su afinamiento, se han intentado evitar ambigüedades y toma como referencia la información experimental proporcionada por Alemán y Masta (2006) complementada por el método propuesto por CEMEX y por el ACI (2015), el mismo que se utilizó para la presente investigación.
Objetivo
Diseñar la dosificación para preparar un metro cúbico de mortero de resistencia f’c = 182 Kg-f/cm2, con asentamiento de 160 mm (CEMEX, 2015) en el cono de Abrams (concreto magro). Se empleará como insumos el cemento Portland CPC, agregado arena, cuya granulometría debe tener un tamaño máximo de 4 mm, un peso volumétrico aparente (incluidos los espacios vacíos) de 1.920 kg/m y una densidad de 1.95 gr/cm3.
Procedimiento
Se estima una resistencia característica deseada, que fue de 140 kg/cm2 y se aplicó lo indicado en la Tabla 3 de Control de Calidad. Se calcula la resistencia media del concreto f’m, que siempre será superior a su resistencia característica. Se eligen 240 kg de agua de la Tabla 4 asumiendo un asentamiento de entre 150mm y 180mm, para un agregado máximo de 10mm, además se obtiene el porcentaje de aire atrapado.
Tabla 3 Tabla control de calidad
Tipo de | Desviacion |
---|---|
control | estandar (σ) |
Muy bueno | 0.07 fm |
Bueno | 0.14 fm |
Regular | 0.21 fm |
Deficiente | 0.28 fm |
Fuente: Elaboración propia
Tabla 4 Cantidad aproximada de agua de mezclado para diferentes asentamientos y tamaños máximos de los agregados
Revenimiento | Cantd de agua(Kg/m3 de concreto para agregados tamaño máximo) | |||||||
---|---|---|---|---|---|---|---|---|
(mm) | 10 | 12.5 | 20 | 25 | 40 | 50 | 70 | 150 |
mm | mm | mm | mm | mm | mm | mm | mm | |
30 a 50 | 205 | 200 | 185 | 180 | 160 | 155 | 145 | 125 |
80 a 100 | 225 | 215 | 200 | 195 | 175 | 170 | 160 | 140 |
150 a 180 | 240 | 230 | 210 | 205 | 185 | 180 | 170 | – |
Aire atrapado | 3 | 2.5 | 2 | 1.5 | 1 | 0.5 | 0.3 | 0.2 |
Fuente: Manual de Practicas de Laboratorios de Concreto de la UACH
Se puede estimar de la Figura 2, tomada del libro Propiedades del Concreto de Neville, que se ve arriba a la izquierda, para una resistencia media de 182 kg/cm2, medida a los 28 días.
Se sustituye el dato de 240 kg de agua en peso de la Tabla 4, en la formula descrita abajo, además se obtiene el porcentaje de aire atrapado del 0.03m3 de esta misma tabla.
De la curva agua/cemento se identificó que para 182 kg/cm3 corresponde una relación agua/cemento de 0.80.
Peso de agua / peso de cemento = 0.80
El contenido de cemento será:
Peso de cemento = peso de agua / 0.80 = 240/0.80=300 kg de cemento
Se trabaja con las siguientes densidades:
Peso de cemento suelto = 1,505kg/m3
Peso de arena compactada seca = 1,920kg/m3
Peso del agua = 1,000kg/m3
Volumen cemento = 300kg/1505kg/m3=0.19m3
Volumen agua=240kg/1000kg/m3=0.24m3
Volumen de aire atrapado = 0.03kg/1000kg/m3= 0.03 m3
Se calcula el volumen de la arena:
Volumen de la arena seca = 1.000 m3- (0.190m3- 0.24m3- 0.030 m3)
Volumen de la arena seca = 0.54m3
Se calcula el peso de agregado de la arena seca:
Peso arena seca= (0.54 m3) (1.92 x 1000 Kg/ m3)= 0.54x1.92x1000= 1,036.8kg
Con los resultados obtenidos se procedió a definir el diseño de las proporciones de insumos para emplearse en cada uno de los especímenes, utilizándose la relación agua /cemento de 0.8 (Tabla 5), lo cual nos permitió realizar diversas combinaciones con distintos valores comprendidos entre 0.60 y 0.80, considerando también que el hierro y la zeolita demandan incluir más agua en el momento de ser incluidos en la mezcla para hacerla más trabajable.
Tabla 5 Proporciones de diseño de insumos para Morteros de junteo mejorados
Proporciones en volumen para preparar un m3 | Dosificación en peso | Dosificación en peso | Dosificación en volumen | |
---|---|---|---|---|
Arena | 0.54 | 1036.8gr | 3.45 | 2.84 |
Cemento | 0.19 | 300.0gr | 1.00 | 1.00 |
Agua | 0.24 | 240.0gr | 0.80 | 0.44 |
Aire | 0.03 | 0 | 0 |
Fuente: Elaboración propia
Etapa experimental
La etapa experimental se desarrolló en 3 fases (Tabla 8). En todas se consideró como dato de referencia el valor mínimo admitido de resistencia a compresión de 5.20 Mpa, según lo prescribe la Norma ASTM C-270. Es pertinente mencionar las siguientes consideraciones:
Tabla 6 Dosificación para muestra de control también denominada “Morteros Estándar”
Denominación | Material | Dosif. en volumen | %peso por dosificación | Especificaciones Técnicas |
---|---|---|---|---|
Aglomerante | Cemento | 1 | 25% | Cemento Portland Compuesto |
Agregados | Arena | 3 | 75% | Arena de 2.5mm de granulometría |
Líquidos | Agua | 0.60 | Agua potable de preferencia |
Fuente: Elaboración propia
Tabla 7 Descripción de los especímenes
Especímenes Cilindricos | Para pruebas SEM | *Los especímenes C-14, C-15 y C-16 destinados a muestras patrón | |
triturados | |||
Especímenes | 14 (C-1 al C-11 y del | 02 ( C-12 Y C-13) | |
cilíndricos | C-14 al C-16* | ||
Total | 16 Especímenes |
Fuente: Elaboración propia
Tabla 8 Guía para la comprensión de la parte experimental. *Los aglomerantes representan 100% y los agregados suman también 100%, por lo tanto, la suma de valores de cemento y zeolita dan 100 y la suma de arena y hierro también dan 100. Pero siempre el peso de los agregados es 3 veces el del aglomerante. Para este estudio se estimó una resistencia límite mínima aceptable de 5.20 Mpa según la Norma ASTMC-270 y ASTM C-780 aplicados en cilindros de D=5cm x H=10c
Estrategia utilizada para analisis | Grupo de muestras | Descripción | Relación | % de Dosificación en peso* | Situación | Observaciones | Resistencia obtenida en MPa | ||||
agua/cemento | Aglomerante | Agregados | |||||||||
cemento | zeolita | arena | hierro | ||||||||
C-1** | 0.52 | Resultados dentro del límite requerido | 12.80 Mpa | ||||||||
Se utilizó la misma | Primera | C-2** | 0.64 | Se | 15.20 Mpa | ||||||
dosificación de materiales áridos y | Serie de resultados: | Trituraron a los 28 | Resultados dentro del límite requerido | ||||||||
diferentes proporciones de agua | Cilíndricos | C-3** | 0.68 | 80 | 20 | 70 | 30 | días | Resultados dentro del límite requerido | 15.84 MPa | |
D-1*** | 60 | 40 | 98.5 | 1.5 | Resultados dentro del límite requerido | 6.35Mpa | |||||
D-2*** | 55 | 45 | 94 | 6 | 8.20MPa | ||||||
Se utilizó diferente | Segunda serie de resultados | D-3*** | 65 | 35 | 94 | 6 | Se | 10.14Mpa | |||
dosificación de materiales | Cilíndricos | Trituraron a los | |||||||||
áridos y las misma | Sin | 0.50 | 28 días | Resultados dentro del límite requerido | |||||||
proporción de agua | Reductor de agua | ||||||||||
D-4*** | 75 | 25 | 96 | 4 | Resultados dentro del límite requerido | 18.31Mpa | |||||
Resultados dentro del límite requerido | |||||||||||
D-5*** | 0.75 | 60 | 40 | 98.5 | 1.5 | Resultados dentro del límite requerido | 6.33Mpa | ||||
D-6*** | 0.70 | 55 | 45 | 94 | 6 | Se | Resultados dentro del límite requerido | 5.40Mpa | |||
Se utilizó diferente dosificación | Cilindricos | D-7*** | 0.80 | 65 | 35 | 94 | 6 | Trituraron a los 28 | Resultados dentro del límite requerido | 7.70MPa | |
de materiales secos y diferentes | Tercera serie de resultados | Con | D-8*** | 1.26 | 65 | 35 | 94 | 6 | días | Resultados dentro del límite requerido | 4.90MPa |
proporciones de agua | Reductor de agua | D-9 | 0.77 | 75 | 25 | 96 | 4 | Para SEM | No se trituro | Microfotografía | |
D-10 | 1.26 | 65 | 35 | 94 | 6 | Para SEM | No se trituro | Microfotografía | |||
Se utilizaron materiales | Espécimen Standard | D-11** | 0.77 | 25 | 0 | 75 | 0 | Se | Resultados dentro del límite requerido | 30.98MPa | |
convencionales cemento, | Espécimen Standard | D-12** | 0.77 | 25 | 0 | 75 | 0 | Trituraron a 28 días | Resultados dentro del límite requerido | 20.00Mpa | |
arena y agua | D-13** |
Nota: ** Las Muestras C-1, C-2, C-3. D-11, D-12 y D-13 Se encuentran en la Tabla 10
*** Las Muestras D-1, D-2, D-3 y D-04 Se encuentran en la Tabla 11 y Las Muestras D-5, D-6, D-7 y D-8 se encuentran en la Tabla 12
Fuente: Elaboración propia.
El contenido de este articulo se enfoca en el estudio y la interpretación de los resultados encontrados en las pruebas de rompimiento de los especímenes obtenidos de las mezclas cementicias mejoradas, cuando han pasado 28 días después de haber sido preparados con nuevos materiales cementantes.
También se tiene en cuenta que la zeolita, al ser un insumo que es lento en alcanzar dureza, según lo revelan estudios experimentales previos a este artículo (Andrada et al., 2011). A efectos de descubrir nuevos comportamientos y tener más seguridad de sus propiedades, se hicieron las roturas de todas las fases luego de 28 días.
Se programó una dosificación específica para todas las muestras patrón o estándar (Tablas 6 y 7).
Primera serie de resultados
En esta primera fase se prepararon 6 especímenes de D= 5cm x H= 10cm, 3 con mortero estándar y 3 con morteros mejorados. Los especímenes mejorados fueron C-1, C-2 y C-3 y sus pesos respectivos fueron 418.73gr, 420gr y 417.5gr, mientras que el peso de los especímenes estándar fue de 421gr, respectivamente. Los 6 se fabricaron simultáneamente y se sometieron a compresión a los 28 días. En esta etapa se empleó mayor cantidad de zeolita y hierro en los especímenes mejorados que en las otras 2 etapas o series subsiguientes, también fue la que mejores resultados demostró en las fases de resistencia a la compresión. Se uniformizó la dosificación de insumos secos del mortero mejorado para los 3 especímenes, pero se hicieron diferentes proporciones de agua para cada uno (Tabla 9).
Tabla 9 Primera muestra de espécimen mejorado Tipo prismático 1
PRIMERA SERIE DE RESULTADOS: Fecha 06/06/2016 | ||||||
---|---|---|---|---|---|---|
Espécimen cilindrico C-1: Dimensiones: D= 5cm x H=10cm | ||||||
Denominación | Material | Dosificación | Dosificación | % de hierro y zeolita | Porcentaje en | % respecto a la |
en gramos | en aglomerantes Z | gramos | mezcla en seco | |||
Aglomerantes | Cemento | 1 | 104.68gr | 80.00% | 83.75gr | 19.98% |
Zeolita | 20.00% | 20.00% | 20.93gr | 04.99% | ||
Agregados | Arena | 3 | 314.05gr | 70.00% | 219.83gr | 52.51% |
Hierro | 30.00% | 94.210gr | 22.50% | |||
Líquidos | Agua | a/c=0.52 | 54.43gr | 100% | ||
Peso | TOTAL | 418.73gr | ||||
Resistencia a la Compresión: 128.75KG-F/CM2=12.80 MPA | ||||||
Espécimen cilindrico C-2 : Dimensiones: D= 5cm x H=10cm | ||||||
Denominación | Material | Dosificación | Dosificación | % de hierro y zeolita | Porcentaje en | % respecto a la |
en gramos | en aglomerantes Z | gramos | mezcla en seco | |||
Aglomerantes | Cemento | 1 | 104.68gr | 80.00% | 83.75gr | 19.98% |
Zeolita | 20.93gr | 04.99% | ||||
Agregados | Arena | 3 | 314.05gr | 70.00% | 221.13gr | 52.51% |
Hierro | 30.00% | 94.210gr | 22.50% | |||
Líquidos | Agua | a/c=0.64 | 66.99gr | 100% | ||
Peso | TOTAL | 420.00gr | ||||
Resistencia a la Compresión: 152.18KG-F/CM2=15.20 MPA | ||||||
Espécimen cilindrico C-3: Dimensiones: D= 5cm x H=10cm | ||||||
Denominación | Material | Dosificación | Dosificación | % de hierro y zeolita | Porcentaje en | % respecto a la |
en gramos | en aglomerantes Z | gramos | mezcla en seco | |||
Aglomerantes | Cemento | 1 | 104.68gr | 80.00% | 83.75gr | 19.98% |
Zeolita | 20.00% | 20.93gr | 04.99% | |||
Agregados | Arena | 3 | 314.05gr | 70.00% | 218.63gr | 52.51% |
Hierro | 30.00% | 94.210gr | 22.50% | |||
Líquidos | Agua | a/c=0.68 | 71.18 gr | 100% | ||
Peso | TOTAL | 417.50gr | ||||
Resistencia a la Compresion:158.43KG-F/CM2=15.84MPA | ||||||
Espécimen cilindricos con Mortero Estándar D-11, D-12 y D-13 | ||||||
Denominación | Material | Dosificación | Dosificación | % de cemento y arena en | Porcentaje en | % respecto a la |
en gramos | aglomerantes y agregados | gramos | mezcla en seco | |||
Aglomerantes | Cemento | 1 | 104.61gr | 25.00% | 104.61gr | 25.00% |
Agregados | Arena | 3 | 314.12gr | 75.00% | 314.12gr | 75.00% |
Líquidos | Agua | a/c=0.60 | 62.76gr | 100% | ||
Peso | TOTAL | 421.00gr | ||||
Resistencia a la Compresión: D-11 presentan 30.98 Mpa y D-12 y D-13 presentan 20.00Mpa |
Fuente: Elaboración propia
Segunda serie de resultados
En esta segunda fase se prepararon 4 especímenes cilíndricos de D= 5cm x H= 10cm. Los 4 son hechos con mortero mejorado según las dosificaciones tipo W, X, Y y Z, (Figura 1) distribuidos así, D-1, D-2, D-3 y D-4. Los pesos fueron 398gr, 404gr, 454gr y 397gr, respectivamente. Los 4 se elaboraron simultáneamente y se sometieron a compresión a los 28 días. En esta segunda fase se emplearon menores cantidades de zeolita y hierro que en la etapa anterior, buscando 2 objetivos, primero, que los pesos de las muestras mejoradas no fueran superiores a los de las muestras estándar, ya que el empleo de una mayor cantidad de hierro afecta definitivamente en el peso de la muestra, y segundo, encontrar una proporción en peso para la zeolita y hierro, que no permita consumir mucho líquido, como se ve en las muestras de la etapa anterior, pues si bien llegaba a los niveles que la normatividad exigía, demandaba mayor cantidad de agua. Es por ello que se redujo la proporción de agua a todos los especímenes utilizando una relación a/c de 0.50. Los resultados no evidenciaron un aumento de la resistencia, a excepción de la muestra D-4 que dio por resultado un valor aceptable de resistencia a la compresión de 18.31MPa. (Tablas 8 y 10).
Tabla 10 Especímenes cilíndricos sin reductor de agua
SEGUNDA SERIE DE RESULTADOS. Fecha:06 -06- 2016 | ||||||
---|---|---|---|---|---|---|
Espécimen cilíndrico D-01 | ||||||
Denominación | Material | Dosifica. | Dosificación | % de hierro y zeolita en | Porcentaje | % respecto a la mezcla |
en gramos | aglomerantes X | gramos | en seco | |||
Aglomerantes | Cemento | 1 | 104.61gr | 60.00% | 62.76gr | 14.98% |
Zeolita | 40.00% | 41.84gr | 9.98% | |||
Agregados | Arena | 3 | 314.12gr | 98.50% | 309.40gr | 73.89% |
Hierro | 01.50% | 4.71gr | 1.12% | |||
Líquidos | Agua | a/c=0.50 | 52.31gr | 100.00% | ||
Resistencia a la Compresión: 63.55kg-f/cm2= 6.35 Mpa | ||||||
Espécimen cilíndrico D-02 | ||||||
Denominación | Material | Dosifica | Dosificación | % de hierro y zeolita en | Porcentaje | % respecto a la mezcla |
en gramos | aglomerantes W | gramos | en seco | |||
Aglomerantes | Cemento | 1 | 104.61gr | 55.00% | 57.53gr | 13.76% |
Zeolita | 45.00% | 47.08gr | 11.21% | |||
Agregados | Arena | 3 | 314.12gr | 94.00% | 295.27gr | 70.51% |
Hierro | 06.00% | 18.84gr | 4.49% | |||
Líquidos | Agua | a/c=0.50 | 52.31gr | 100.00% | ||
Resistencia a la Compresión: 82.16kg-f/cm2= 8.20 Mpa | ||||||
Espécimen cilíndrico D-03 | ||||||
Denominación | Material | Dosifica | Dosificación | % de hierro y zeolita en | Porcentaje | % respecto a la mezcla |
en gramos | aglomerantes Y | gramos | en seco | |||
Aglomerantes | Cemento | 1 | 104.61gr | 65.00% | 67.99gr | 16.23% |
Zeolita | 35.00% | 36.62gr | 8.74% | |||
Agregados | Arena | 3 | 314.12gr | 94.00% | 295.27gr | 70.51% |
Hierro | 06.00% | 18.84gr | 4.49% | |||
Líquidos | Agua | a/c=0.50 | 52.00gr | 100.00% | ||
Resistencia a la Compresión: 101.40 kg-f/cm2= 10.14 Mpa | ||||||
Espécimen cilíndrico D-04 | ||||||
Denominación | Material | Dosifica | Dosificación | % de hierro y zeolita en | Porcentaje | % respecto a la mezcla |
en gramos | aglomerantes | gramos | en seco | |||
Aglomerantes | Cemento | 1 | 104.61gr | 75.00% | 78.45gr | 18.73% |
Zeolita | 25.00% | 21.55gr | 0.05% | |||
Agregados | Arena | 3 | 314.12gr | 96.00% | 301.55gr | 72.01% |
Hierro | 4.00% | 12.56gr | 0.03% | |||
Líquidos | Agua | a/c=0.50 | 52.31gr | |||
Compresión: 183.10 kg-f/cm2= 18.31 Mpa |
Tercera serie de resultados
En esta tercera fase se prepararon 8 muestras en especímenes cilíndricos. En todos se aplicaron distintas relaciones a/c y distintas dosificaciones en los insumos secos. Como la resistencia a la compresión disminuyo bastante, entonces se optó por elevar la consistencia haciendo más fluida la mezcla aplicando un reductor de agua en los 4 primeros. En el otro grupo de 4 muestras, D-5, D-6, D-7 y D-8 se utilizaron distintas dosificaciones tanto en insumos secos como distintas relaciones de agua/cemento, pero no se aplicó el aditivo ya señalado. Para estas mismas muestras se consideraron porcentajes similares a las del párrafo anterior, el porcentaje de cemento y zeolita fue de 65% y de 35%, respectivamente. Las muestras D-9 y D-10, están destinadas para el análisis SEM. La D-10 tiene la misma relación a/c que la D-8, esta última dio el resultado más bajo de resistencia a la compresión. Las muestras D-11, D-12 y D-13 son morteros estándar (Tabla 11).
Tabla 11 Especímenes cilíndricos con reductor de agua
TERCERA SERIE DE RESULTADOS. Fecha: 07-07- 201 | ||||||
---|---|---|---|---|---|---|
Espécimen cilíndrico: D-5-con reductor de agua de 4cm3 | ||||||
Denominación | Material | Dosifica. | Dosificación en | %de hierro y zeolita en | Porcentaje | %con respecto a la |
gramos | aglomerantes X | gramos | mezcla en seco | |||
Aglomerantes | Cemento | 1 | 104.61gr | 60.00% | 62.76gr | 14.98% |
Zeolita | 40.00% | 41.84gr | 9.98% | |||
Agregados | Arena | 3 | 314.12gr | 98.50% | 309.40gr | 73.89% |
Hierro | 1.50% | 4.71gr | 1.12% | |||
Líquidos | Agua | a/c=0.75 | 78.45gr | 100.00% | ||
Resistencia a la Compresión: 63.3 kg-f/cm2= 6.33 Mpa | ||||||
Espécimen cilíndrico: D-6 -con reductor de agua de 4cm3 | ||||||
Denominación | Material | Dosifica. | Dosificación en | %de hierro y zeolita en | Porcentaje | %con respecto a la |
gramos | aglomerantes X | gramos | mezcla en seco | |||
Aglomerantes | Cemento | 1 | 104.61gr | 55.00% | 57.53gr | 13.76% |
Zeolita | 45.00% | 47.08gr | 11.21% | |||
Agregados | Arena | 3 | 314.12gr | 94.00% | 295.27gr | 70.51% |
Hierro | 6.00% | 18.84gr | 4.49% | |||
Líquidos | Agua | a/c=0.70 | 73.2gr | 100.00% | ||
Resistencia a la Compresión: 54.01kg-f/cm2= 5.40 Mpa | ||||||
Espécimen cilíndrico: D-7 -con reductor de agua de 4cm3 | ||||||
Denominación | Material | Dosifica. | Dosificación en | %de hierro y zeolita en | Porcentaje | %con respecto a la |
gramos | aglomerantes X | gramos | mezcla en seco | |||
Aglomerantes | Cemento | 1 | 104.61gr | 65.00% | 67.99gr | 16.23% |
Zeolita | 35.00% | 36.62gr | 8.74% | |||
Agregados | Arena | 3 | 314.12gr | 94.00% | 295.27gr | 70.51% |
Hierro | 6.00% | 18.84gr | 4.49% | |||
Líquidos | Agua | a/c=0.80 | 83.68gr | 100.00% | ||
Resistencia a la Compresión: 77.04kg-f/cm2= 7.70 Mpa | ||||||
Espécimen cilíndrico D-08- con reductor de agua de 4cm3 | ||||||
Denominación | Material | Dosifica. | Dosificación en | %de hierro y zeolita en | Porcentaje | %con respecto a la |
gramos | aglomerantes X | gramos | mezcla en seco | |||
Aglomerantes | Cemento | 1 | 104.61gr | 65.00% | 67.99gr | 16.23% |
Zeolita | 35.00% | 36.62gr | 8.74% | |||
Agregados | Arena | 3 | 314.12gr | 94.00% | 295.27gr | 70.51% |
Hierro | 6.00% | 18.84gr | 4.49% | |||
a/c=1.26 | 131.79gr | |||||
Resistencia a la Compresión: 49.00kg-f/cm2= 4.90 Mpa |
Fuente: Elaboración propia. “En estas experimentaciones, se consideró uniformizar el mismo peso en seco para preparar todas las muestras que es de 418.71gr
Análisis de los resultados
La máxima cantidad de hierro que se pudo incorporar a la mezcla, respetando los niveles mínimos de resistencia mecánica a la compresión recomendados por las Normas ASTM C-270 y ASTM C-780, es hasta 30% del total del peso de toda la mezcla en seco con una relación a/c 0.64. Para este valor, la máxima resistencia alcanzada fue de 15.20 Mpa. (Tabla 9). La mínima cantidad de hierro que se puede incorporar a la mezcla sin alterar las propiedades de resistencia, ni consumir mucha agua es hasta un 2.5% del total del peso de toda la mezcla en seco, usar menos cantidad, demandaría aumentar más zeolita y eso implica utilizar más agua, el agua necesaria es de una relación 0.50 a/c, para estos valores la máxima resistencia alcanzada fue de 18.31Mpa (Figura 5.1).

Figura 3 Insumos de la Innovación “zeolita, hierro, arena, cemento”, a la derecha, especímenes prismáticos mejorados de la primera etapa experimental, A. Zeolita, B. Hierro, C. Arena y D. Cemento

Figura 4 Representación gráfica de la incidencia del hierro y la zeolita en la propiedad de Resistencia mecánica a la compresión. En la Figura 7.1a, se observa que, a mayor concentración de hierro, disminuye la resistencia. En la Figura 4.2a, se observa igualmente que a mayor concentración de zeolita disminuye la Resistencia. En la tabla de la misma figura puede verse el detalle por espécimen

Figura 5 Representacion grafica de la incidencia de la relación agua/cemento y de los aditivos en la propiedad de la resistencia mecánica a la compresión. En la Figura 5.1a mayormente se observa que a mayor valor de la relación a/c se produce una disminución en la resistencia. Ver el orden ascendente de la relación a/c en la tabla de la misma figura. En la Figura 8.2a, la incorporación de aditivos reductores produce una disminución en los resultados de la Resistencia. Ver detalle en la tabla
Se comprobó que la zeolita y el hierro demandan una mayor cantidad de agua al momento de realizar las mezclas en comparación con los especímenes estándar, con una relación a/c de 0.8. Todos los especímenes de mortero estándar sometidos a la prueba de resistencia, presentaron valores comprendidos entre 20MPa y 30.98MPa, las pruebas se hicieron de acuerdo con el diseño de mezclas con la respectiva prueba de revenimiento. La relación fue de 0.60 a/c.
La metodología empleada para la incorporación del hierro en polvo, fue utilizar en cada ensayo consecutivo proporciones distintas de este mineral, de modo tal que se van haciendo más altos los valores de las proporciones a medida que avanza la experimentación. Los resultados nos permiten identificar 2 fases, en la primera, cuando al adicionar el hierro en cada una de las 2 primeras pruebas, la proporción del mismo se va incrementando de 0.00gr a 4.71gr, dando por resultado que el valor de la resistencia a la compresión aumenta también hasta tomar valores de 18.31 Mpa, mientras la relación a/c toma valores que decrecen de 0.75 hasta 0.6. Luego, cuando al adicionar el hierro en las siguientes pruebas donde las proporciones son superiores a 4.71 gr hasta llegar a 94.21gr, los valores de la resistencia mecánica a los esfuerzos de compresión aumentaron en forma proporcional, entre 6.35MPa hasta 15.84MPa. En este caso, la relación a/c toma valores que ascienden de 0.6 hasta 0.75. (Figuras 4.1a y 4.1b). En cuanto a la adición de la zeolita, también se identificaron 2 fases, cuando la cantidad de la misma incorporada en cada una de las pruebas asciende en proporciones de 0.00gr hasta 21.55gr, el valor de la resistencia mecánica a la compresión comenzó a subir desde 4.90MPa hasta 20MPa. Luego cuando el incremento progresivo de la misma a la mezcla asciende desde 20.93gr hasta 36.62gr, se produce una disminución de la resistencia mecánica a la compresión, desde 15.84MPa hasta 4.90MPa (Figuras 4.2b y 5.2b). Para las situaciones mencionadas arriba se utilizaron las mismas relaciones agua/cemento que para el caso del hierro.
En cuanto a los aditivos reductores de agua, se observó que resultan inconvenientes, pues producen disminución en los valores de la resistencia mecánica (Figura 5.2b)
Conclusiones
La adición de hierro a las mezclas cementicias que contienen cemento, zeolita, arena y agua, permite obtener resultados positivos en las pruebas de resistencia mecánica a los esfuerzos de compresión, ya que superan los niveles mínimos admitidos de 5.20 MPa según lo recomienda las Norma ASTM C-270 y la Norma ASTM C-780.
En términos generales se puede decir que a medida que se incrementan las proporciones de hierro a las mezclas cementicias, se obtienen valores en los resultados de los ensayos a resistencia mecánica a la compresión igualmente ascendentes, aunque esto signifique en la mayoría de los casos, utilizar una relación agua/cemento más alto.
Los resultados de las pruebas de resistencia mecánica a la compresión de las mezclas cementicias que utilizan hierro, zeolita, cemento, arena y agua son aceptables, pero no son tan altos como los obtenidos de las mezclas cementicias de los morteros de pega estándar, debido a que la zeolita y el hierro representan un alto contenido de material fino, consecuentemente su área superficial específica es mayor, y eso demanda un mayor requerimiento de agua para alcanzar consistencia, fluidez y viscosidad.
La consistencia plástica adecuada se define por un asentamiento de 160mm, lo cual permitió diseñar una pasta cementicia trabajable para morteros de pega que alcancen resistencias superiores a 15MPa, este antecedente puede tomarse en cuenta en posteriores investigaciones que aborden temáticas similares sobre el estudio de los morteros de junteo obtenidos de residuos provenientes de la post-minería.