INTRODUCTION
Nowadays cellulose fibers are widely used for reinforcement of mortar, concrete, and polymer composites. Cellulose fiber composites are considered as alternative and competitive materials compared with glass and carbon composites due to their low density, good mechanical properties, eco-friendly nature and low investment cost. Furthermore, the physical and mechanical properties of composites can be improved by chemical treatment (Alawar et al. 2009, Alsaeed et al. 2013, Iucolano et al. 2015, Achour et al. 2017, Oushabi et al. 2017) or by adding a suitable resin to the matrix during its fabrication procedure (Hamzaoui et al. 2014, Fiore et al. 2015, Atiqah et al. 2017, Ghofrani et al. 2017).
In this regard, there are several available works in literature on the use of cellulose fiber materials as reinforcement for concrete and mortar. The natural fibers materials which have been investigated are mainly banana (Iucolano et al. 2015, Mukhopadhyay and Bhattacharjee 2016), bamboo (Agarwal et al. 2014, Javadian et al. 2016, Khatib and Nounu 2017), alfa (Khelifa et al. 2016), flax (Yan and Chouw, 2013, Yan et al. 2014), date palm (Kriker et al. 2005, Benmansour et al. 2014, Djoudi et al. 2014, Boumhaout et al. 2017), etc. Most of these studies revealed that date palm fibers are very promising reinforcing materials and can be used as thermal insulation materials in building.
In Tunisia, the oasis areas, which include cultivated land covered around 45 000 ha in 2010 (Ben Salah 2014). Every year after the date fruit harvesting, a considerable amount of date palm wastes is accumulated in huge mounds that ultimately cause environmental problems. In 2006, a total of 90 000 t of agricultural wastes were generated in oases (ANGED 2006). Palm leaflets are traditionally used to make utensils and basketworks (Hamza et al. 2013). Nowadays the by-products and waste of date palm are also used as a component for compost preparation (Bchini et al. 2002, Sghairoun and Ferchichi 2011, Latigui et al. 2013, El Khaldi et al. 2016).
In the construction sector the uses of these wastes are very limited, however they possess attractive properties compared to synthetic fibers. The valorization of this vegetable waste in the development of the construction sector has several objectives: economic, technical and environmental. Its abundance in nature and mechanical and thermal properties makes possible to classify it among the strategic resources of renewable energies (Sumathi et al. 2007).
Furthermore, gypsum deposits outcrop in thick layers in southern Tunisia and many plaster manufactures are installed in this region. The produced plaster is mainly used for decorative purposes, although it has interesting thermal properties (Mansour et al. 2013). In the present study, the effect of date palm fibers waste (DPFW) as reinforcing agent on the mechanical properties of plaster-based composite was investigated. The results of an alkaline treatment and drying temperature have also been studied.
EXPERIMENTAL STUDIES
Materials
Plaster
The plaster (DecoM2) used in this study was provided by the SIPS company and is ISO 9001 certified. The setting behavior of the plaster was characterized by common penetration procedures (knife cut for the initial setting and 40 shore C for the final setting) according to French standard NF B12-401. The grain size distribution was determined using wet sieving (Table I). The physical and mechanical properties of used plaster are presented in table II and figure 1.
TABLE I GRAIN SIZE DISTRIBUTION OF THE STUDIED PLASTER
Grain size | Percentage |
+ 250 µm | ≤ 0.2 % |
-250 + 150 µm | 1 to 2.5 % |
-150 + 090 µm | 12 to 17 % |
-90 + 063 µm | 22 to 28 % |
TABLE II PHYSICAL PROPERTIES OF THE STUDIED PLASTER
Parameter | Value |
Initial setting (min) | 13 |
40 shore ºC for final setting (min) | 30 |
Compressive strength (MPa) | 9.2 |
Flexion strength (MPa) | 4.2 |
Water absorption (%) | 35 |
Porosity (%) | 38 |
Palm date fibers
The ground palm wastes were provided by Chenini Oasis Backup Association, Gabes. Two types of treatment were applied to the raw fibers. In the first one, sodium hypochlorite was used for 2 h, and the second one consisted of impregnation in an NaOH solution at various concentrations (1 %, 2 % and 4 %) for 24 h. The incorporated fibers were treated in order to clean the surface from impurities and to protect it against water.
The thermal analysis of biomass was conducted in a thermogravimetric analyzer (model SETARAM). The DTG curve (Fig. 2) revealed three distinct endothermic peaks corresponding to the decomposition of palm waste:
In the first zone (25-200 ºC) endothermic evaporation of residual water occurred, corresponding to a mass loss of absorbed moisture of approximately 1 %.
The second zone (200-300 ºC) is characterized by significant mass loss (about 3.5 %) due to hemicellulose decomposition (Yang et al. 2004).
The third zone (300-400 ºC) corresponds to the stage of decomposition of cellulose.
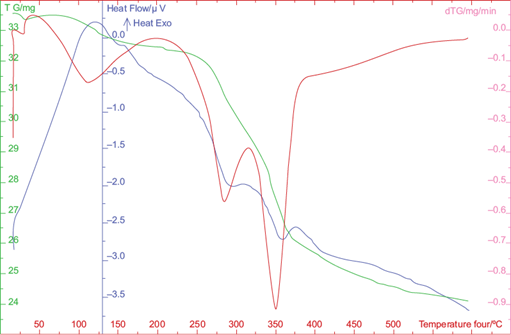
Fig. 2 Thermal analysis of date palm fibers. Thermogravimetry (TG) in mg = sample loss weight during heating (green curve); DTG/mg/min = the first derivative of TG (purple curve); DSC = differential scanning calorimetry (heat flow/µv; blue curve). Horizontal axis is temperature (ºC)
The decomposition of lignin took place over a wide range of temperatures up to 400 ºC (Nasser et al. 2016). The microstructures of the palm fiber show that its surface is irregular with many filaments, impurities and pores (Fig. 3a, c).
Analytical methods
The gypsum composite was prepared using variable mass proportions of DPFW (7, 10, 15, 17, and 20 %). To measure the mechanical strengths, standard prismatic test pieces of 4 × 4 × 16 cm were manufactured with a constant water plaster ratio (W/P) of 0.65. These tests were conducted at ages of 3, 7 and 28 days. The capillary water absorption coefficient of hardened mortar was determined according to the BS EN 1015-18 method of test. In order to determine the thermal conductivity of the samples, a Taurus TLP300 Thermal Conductivity Analyzer was used.
RESULTS AND DISCUSSION
Mechanical strength
The results of flexural strength are presented in figure 4a, b. There were not relevant effects of the fibers on the flexural strength from day 3 to 28, except for the sample incorporating 17 % of fibers in the formulation. The last sample shows an enhancement in mechanical properties at different ages compared to the reference composite. At day 28, the improvements were approximately 11 % for this sample.
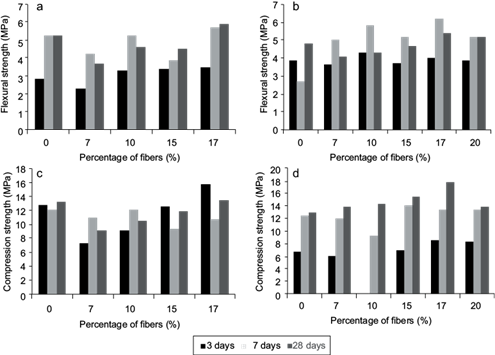
Fig. 4 Flexural and compressive strength results of tested composites. (a and c) Before washing; (b and d) after washing
The results of the compression tests before and after washing are presented in figures 4c and 3d, respectively. An increase in the compressive strength is noted for all composites compared to the control mortar. At day 28, the compressive strength of the composite with 17 % of fibers was 26 % higher than the reference without fibers. The amelioration in the compressive strength is also attributed to a better fiber-matrix adhesion, since fibers become rougher and thinner after cleaning with water, which may improve their adhesion ability with the matrix (Sawsen et al. 2015).
The addition of 17 % of fibers with different lengths influences the rheological behavior of the plaster. The reduced flexural strength is generally caused by the loss of maneuverability, which is due to poor distribution of the fibers in the fresh state and leads to increasing porosity. Concerning the compressive strength, there is a slight improvement, reaching a maximum for fiber lengths of 20 mm and then a slow decrease for the lengths of 30 and 40 mm (Fig. 5). This decrease may be due to unsuitable compactness and workability caused by excess of fibers in the mixture.
Alkaline treatment
From the previous tests, we found that an addition of 17 % of fibers gives the best results in terms of flexural and compressive strengths. Hence, we incorporated this percentage of fibers in order to develop the resto of the tests.
The mechanical properties of the studied fibers before and after the treatment with different percentages of NaOH are shown in table III. An improvement in the flexural strength of the DPFW was observed when the alkali treatment was applied. This enhancement can be explained by the removal of the significant parts of lignin, hemicelluloses, wax and oils covering the external surface of the fibers (Li et al. 2007). This modification facilitates the rearrangement of fibrils (Fig. 3b, d) along the direction of flexural deformation. Furthermore, the improvement of strength can be due to the increase of cellulose content and the compactness of the fibers (Sathishkumar et al. 2013).
Water absorption
Figure 6 shows a correlation between the increasing percentages of DPFW, which tend to increase water absorption. Increasing the percentages of DPFW from 7 to 20 % in the plaster mortar resulted in an increase of water absorption. This behavior is attributed to the porosity of fibers and their hydrophilic character, which is mainly due to the presence of hemicelluloses.
Plaster tiles of dimension 300 x 300 x 20 mm were made. After immersion in water, the differences in water absorption were minimal (Table IV). However, the absorption increases respectively to 34.84 and 34.41 % for the specimen reinforced with DPFW and for treated fibers. The treatment with epoxy resin decreases water absorption. This decrease is due to the surface modifying treatment and thereby, hydrophilic behavior is relatively reduced (Sreekala et al. 2002).
Comparison with natural insulating composites
Table V shows the comparison of thermal conductivity of some composites made with natural fibers and used as construction materials for thermal insulation. The experimentally measured values indicate that the prepared composite in this study presents an excellent thermal performance compared to other composites, as shown in the literature.
TABLE V COMPARISON OF THERMAL CONDUCTIVITY AND DENSITY OF DPFW WITH SOME MATERIALS USED FOR THERMAL INSULATION IN THE BUILDING
Composite | Thermal conductivity (W/mK) | r kg/m3 | References |
Plaster + 17% DPFW | 0.52 | 1415.15 | This study |
Gypsum neat | 0.44 | 1130 | Chikhi et al. 2013 |
Date palm | 0.072-0.085 | 187- 389 | Asdrubali et al. 2015 |
Plaster concrete | 0.89 | 1890 | Djoudi et al. 2014 |
Plaster concrete + 2 % DPFW | 0.76 | 1200 | Djoudi et al. 2014 |
Concrete + cork 10 % | 0.96 | 2100 | Panesar et al. 2012 |
DPFW: date palm fibers waste composites
According to Djoudi et al. 2014, the thermal conductivity decreases when fiber content increases. The recent study elaborated by Braiek et al. 2017 mentioned that this composite material has good thermophysical properties and can be used in walls or false ceilings. Furthermore, the length of the fibers influences the thermal conductivity; the composite made with short fiber produces many voids, hence leading to low thermal conductivity. The studied composite can be considered as a lightweight material. This value is in the range of data reported in the literature on aggregate concrete, which varied from 0.3 to 0.6 W/mK. This indicates a promising potential for the development of efficient and safe building insulation materials.
Effect of drying temperature
The rheological behavior shows the same evolution at a drying temperature of 40 and 60º C. The flexural and compressive strengths increase with the drying time (Fig. 7). However, these parameters exhibit a large drop for a drying time of 24 h at 80 ºC (flexural = 0.234 MPa, compression = 3.65 MPa).

Fig. 7 Flexural and compressive strength results of tested composites under different drying temperatures
The increase of mechanical properties can be explained by the acceleration of the curing mechanism of the plaster induced by drying temperature and the increase of fiber-matrix adherence. Nevertheless, high temperature (80 ºC) leads the release of volatiles, discoloration and poor mechanical properties.
CONCLUSION
This experimental study investigated the incorporation of DPFW as reinforcement in a plaster matrix. After carrying out several tests, the optimal percentage of fibers was 17 %, and the length was 20 mm.
The incorporation of DPFW improves mechanical strength with the increasing percentage and length of the fibers compared to a control plaster without them. However, a slight reduction was recorded for a certain percentage due to the loss of workability and lousy orientation of the fibers and the same results for the compressive strength.
The treatment with NaOH showed an enhancement in the rheological properties (flexion and compression) of the biocomposite and reduced the retardation effect by removing impurities and some soluble compounds. Furthermore, the epoxy treatment effectively contributed to reducing water absorption. The physical properties showed more porous and hydrophilic fibers, possessing high absorption capacity.
In the second part of the experimental study, the drying test at different temperatures on the reinforced-fiber plaster had the following results:
The flexural and compressive strength increased progressively as a function of time, which can be explained by the development of plaster hardening and the increase adhesion between matrix and fiber.
It was demonstrated experimentally that the addition of 17 % DPFW produced a composite with k = 0.52 Wm-1K-1 and r = 1415 kg m-3. According to these results, the studied biocomposite can be used as sustainable insulation material in building structures.