1. Introduction
Over the past decades, the role of coal as an energy source has been indispensable because of its proven stability in supply and cost. Besides the liquid fuels, coal remains the second most consumed fossil fuel whose current world total consumption stands around 160 quadrillion Btu and it is expected to increase to 180 quadrillion Btu in the year 2040 (US EIA, 2016).
Coal has been identified as the most abundant fossil fuel in China (Duan et al., 2016). Moreover, China leads the rest of the world in the production and consumption of coal with 3527 Mtoe production capacity representing about 46% of the total world production in 2015 and total consumption greater than 80 quadrillion Btu which accounts for 49% of the current world's total coal consumption (IEA, 2016; US EIA, 2016).
Nearly half of the world’s coal reserves consists of low rank coal (Fujitsuka, Ashida, Kawase, & Miura, 2014; Kang et al., 2013), which has reportedly become highly competitive in the energy market because of its attractive properties (Sun, Chen, Wang, Lin, & Wang, 2015). However, low rank coal usually contains high moisture content (25 - 60%), which poses serious environmental problems as a result of CO2 emission from combustion (Kang et al., 2013; Morimoto, Nakagawa, & Miura, 2009; Tay, Kajitani, Zhang, & Li, 2013). Therefore, there has been increasing interest in developing efficient and environmentally friendly technologies to utilize the low-rank coal (Duan et al., 2016; Fujitsuka et al., 2014).
Coal gasification has particularly been considered as one of the most important and versatile clean coal technologies for purposes such as the generation of electricity and the production of chemicals, liquid fuels and hydrogen (Li, 2007; Xu et al., 2015). Coal gasification has also been reported as an efficient way to produce important fuel such as syngas and to reduce the pollutant emission during coal utilization (Li, Dai, Yang, Yu, & Wang, 2015). Specifically, because of the high volatility and reactivity of the low rank coal, gasification technology is a key route to its efficient and environmentally friendly utilization (Sun et al., 2015; Xu et al., 2015). Moreover, low rank coal has been identified as a very good gasification feedstock due to its important characteristics including abundant oxygen-containing functional groups, a proportionally larger transition pore and macropore structure, and more inorganic catalytic constituents (Sun et al., 2015) that allow it to be gasified at lower temperature (Jing, et al., 2013; Li, 2007).
Some recent research efforts on advancement in coal gasification technologies have considered the effects of process factors such as heating rate and CO2 concentration with the aim of improving the gasification efficiency (Guizani, 2014; Jayaraman, Gokalp, Bonifaci, & Merlo, 2015; Liu, Tate, Bryant, & Wall, 2000; Tian, Qiao, Tian, & Liu, 2016). From some of these works, the use of CO2 as a gasifying gent has been observed to effectively increase the carbon conversion and the CO yield while decreasing that of H2 (Guizani, 2014; Jayaraman et al., 2015). Similarly, it has been reported that the purpose of increasing the heating rate is to improve gasification efficiency (Fushimi, Goto, Tsutsumi, Hayashi, & Chiba, 2003; Jayaraman et al., 2015).As observed by Guizani (2014) and Fushimi et al. (2003), during coal gasification,char production is maximized at low temperatures and slow heating rate conditions and, as the temperature and heating rate increase, more light gases are produced, the general effects that may hinder the gasification efficiency. Furthermore, according to Fushimi et al. (2003), under the slow heating rate of gasification of low rank coal, steam reacted with the metaplast and promoted the evolution of tar above the temperature of 623K. In comparison, however, when the heating rate was high, steam reforming of volatile matter and steam gasification of metaplast took place parallel to metaplast formation and condensation; and thus the char produced was almost completely gasified and converted into H2 and CO2 by steam. By doing so, the chemical energy of coal was mainly converted into hydrogen energy and the gasification efficiency was therefore increased (Fushimi et al., 2003; Jayaraman et al., 2015).
However, despite the advantages highlighted above, studies on gasification of low rank coal using rapid heating rate and CO2 as a gasification agent have not received adequate attentions. Therefore, the present study aims at investigating the gasification characteristics of low rank coal in a CO2-rich environment and high heating rate. Ultimately, suitable gasification conditions for effective results will be obtained by numerical simulation using the CMG STARS.
2. Experimental section
As a first step on determining the suitability of low rank coal, experiments to test the gasification potential of the coal samples were conducted to compare the weight loss and CO2 emissions from the gasification of Shandong low rank coal and the Datong coal under air and CO2-rich conditions at different pressures. Then, gasification experiments were run under CO2-rich environments to obtain the parameters for model development. In addition, a thermo-gravimetric analysis (TG-DTA) was carried out on the low rank coal to obtain the kinetics parameters. The gasification experimental data and the kinetic parameters were used in developing the simulation model using the CMG STARS advance simulator. Subsequently, simulation studies were performed to determine the effective heating rate, pressure and CO2 concentration for the gasification of the Shandong low rank coal. The sequence of experimental procedures is shown in Figure 1.
2.1 Pretreatment and proximate analysis
The coal samples used in this work were obtained from two different coal mines in China. The lignite (low-rank) coal was mined from Shandong (designated SD), while the bituminous coal sample was obtained from Datong coal mine (designated DT). The coal blocks were pulverized and sieved to average particle sizes of 0.5 mm using a grinder and a standard sieve (35 mesh size). The pulverized coal particles were stored in an air-tight container to prevent contamination before the experiment. Then, proximate analysis was carried out on the coal sample using a high-temperature furnace (NPC-TO2). Compositional analysis to determine the pertinent properties including moisture content, ash content, volatile matter, and fixed carbon content was carried out following the standard ASTM procedures. Each procedure was repeated 3 times; and the average data was calculated as the final result.
2.2 TG-DTA analysis and coal gasification experiment
The thermo-gravimetric and differential thermal analysis (TG-DTA) was carried out using 30 mg of the pulverized sample of the low rank coal at a temperature ranging from 22 to 800 °C and the heating rate of 10 °C/min using a BRUKER 2000SA TG-DTA analyzer (Massachusetts, United States).
As shown in Figure 2, the coal gasification experiment essentially comprises a laser beam generator, a gasification vessel, and a gas chromatography (GC) system for the flue gas analysis. The gasification reactor is made up of a cylindrical glass vessel, and two gas tanks which were installed to control the inner gas environment and pressure. The coal sample was heated in the glass vessel at standard atmospheric pressure and with increasing pressure of air or CO2 gas. The vessel temperature was heated at 1000 oC, the 25 mg of coal sample fed into the ceramic container was placed at the bottom of the vessel with adiabatic material to prevent heat or matter transfer.
The vessel was sealed with a ZnSe filter to allow the passage of the laser beam (10 W, for 1 min). After the combustion, gas in the vessel was collected for a component analysis using a GC-14B gas analyzer. Prior to gas analysis, the machine was calibrated using standard CO, H2, CH4, and CO2 gas. Each gasification experiment was repeated 5 times, and the average data was calculated as the final result.
2.3 Model development using CMG stars and numerical simulation
The model employed for the simulation of the gasification process was built using the CMG STARS (Computer Modeling Group Ltd.) simulator which is usually employed in advanced petroleum reservoir simulation for thermal enhanced oil recovery (TEOR) processes. Previous researchers have employed the software in the numerical simulation and feasibility studies of the underground coal gasification (UCG) system for Alberta coal seam (Kariznovi, Nourozieh, Abedi, & Chen, 2013; Nourozieh, Kariznovi, Chen, & Abedi, 2010).
2.3.1 Stoichiometry of coal gasification reactions and gasification kinetic parameters
Chemical reactions as well as stoichiometric data previously presented by Nourozieh et al. (2010) and Kariznovi et al. (2013) were used in the simulation studies (see Table 1). The kinetics parameters, i.e., the activation energy (Ea) and reaction pre-exponential factor (A), for the gasification process were obtained from the TG-DTA data using the non-isothermal analysis (Alonso, Alvarez, Borrego, Menendez, & Marban, 2001; Jankovica & Smičiklas, 2011) and the composite differential method (Jankovica & Smičiklas, 2011; Moon et al., 2013; Ren et al., 2014).
Table 1 Chemical kinetic parameters for numerical simulations (adapted from Kariznovi et al., 2013; Nourozieh et al., 2010).
Chemical reactions | A (min-1) | E a (kJ/mol) |
---|---|---|
(b) O2 + C → CO2 | 1250 | 100 |
(c) CO2 + C → CO | 4.44 x 106 | 249 |
(d) H2O + C → CO + H2 | 1.26 x 104 | 156 |
(e) 2H2 + C → CH4 | 1.04 x 1011 | 200 |
(f) 0.5O2 + CO → CO2 | 4.5 | 247 |
(g) H2O + CO → CO2 + H2 | 1.67 x 104 | 12.6 |
(h) CO2 + H2 → H2O + CO | 5.67 x 104 | 12.6 |
(i) H2O + CH4 → CO + 3H2 | 5.88 x 103 | 30 |
(j) CO + 3H2 → H2O + CH4 | 1.88 x 104 | 30 |
Subsequently, a 3-D cylindrical gasification model was built based on the information obtained. The cylindrical model was determined as the real size of the gasifier vessel used in the experiment; the parameters were also determined to fit the real experiment. The simulation conditions and 3-D gasification model are presented in Table 2 and Figure 3, respectively. The pressure and water saturation in the operating parameter can be adjusted to create different simulation environments for gasification. The model was built with the consideration that the coal sample was at the center block of the bottom layer (1:5, 1:4, 21:25), and by setting the heat point at the middle of the coal sample (1:2, 1:4, 23:24). Each simulation run was set to heat for 2 min, and heating was stopped for 30 s before calculating the production from the producer part of the model.
Table 2 Model Parameters for IGCC Gasification Simulation.
Parameter | Value |
---|---|
Reservoir temperature | 20 - 1000 oC |
Reservoir pressure | 0.1 - 1.7 MPa |
Coal Permeability | 1 mD |
Coal porosity, fraction | 0.973 |
Initial water saturation, fraction | 0.0265 |
Injected fluid | Water/oxygen |
Number of grids (uniform) | 1728 |
Heat power | 37.5 J/s |
Mass of coal | 25 mg |
3. Results and discussion
3.1 Proximate analysis of the coal samples
Several factors including coal rank or quality, structural properties of char and their variation during the gasification reactions have been reported in the literature to have influence on the gasification reactivity of coal (Clemens, Damiano, & Matheson, 1998). The results obtained from the compositional analysis of the Shandong (SD) low-rank coal, as presented in Table 3, show that it has higher moisture content but less carbon content compared with the Datong (DT) bituminous coal. This indicates that the combustion of low-rank coal could lead to higher emission of CO2 gas. However, it can be observed from Table 3 that the Shandong coal contains higher volatile contents than the Datong coal. It is therefore expected that Shandong coal will show higher efficiency as gasification feedstock compared with the Datong coal sample.
3.2 Gasification potential of the coal samples
The gasification characteristics of the coal samples were compared in terms of weight loss resulting from the combustion in air and CO2 environments. The change in weight loss with pressure under air and CO2 gasification conditions is presented in Figure 4(a), while Figure 4(b) compares the cumulative CO2 production from the Shandong (SD) low rank coal with the production from Datong (DT) coal under air gasification and increasing pressure.

Fig. 4 (a and b): Comparison of gasification characteristics of Shandong (SD) low rank coal and Datong (DT) bituminous coal.
From Figure 4(a), it can generally be observed that the mass loss in the low rank (SD) coal is higher than that of the Datong bituminous coal sample. Under air gasification conditions, the mass loss observed in the Shandong low rank coal is 61% at 0.1 MPa, while the DT coal sample is 50% at the same pressure. Likewise, the mass losses are 70% and 68% at a pressure of 1.7 MPa for the Shandong coal and Datong coal, respectively. These results also show that the higher the pressure, the higher the weight loss for the process under air gasification condition.
On the other hand, under CO2-rich condition, although Shandong coal consistently lost more weight than the Datong coal sample, it can be observed that the weight loss decreased with increasing the pressure and was lower than the weight loss under an air gasification environment for both samples.
The higher weight loss of the Shandong (SD) low rank coal is susceptibly due to the presence of higher moisture and volatile contents as shown in Table 3. Accordingly, during heating, more moisture and volatile matter contents were easily lost. In addition, the combustion reaction in CO2 environment was lower than that in air due to the absence of O2.
In general, as observed from Figure 4a, the trends are susceptibly a result of higher volatile contents of the low rank coal compared to the bituminous coal. Also, complete combustion is expected in the presence of air compared to a CO2 environment. In the presence of air, the weight loss became higher as the system pressure increased susceptibly due to the effect of pressure on the rate of the combustion reaction. However, the weight loss was observed to decrease significantly because of increasing the pressure of CO2, probably as a result of the effect of carbon deposition which can retard the reaction rate. In addition, From Figure 4b, the higher CO2 production from the Shandong low rank coal, as expected, is susceptibly due to the higher moisture content compared to the bituminous coal.
Moreover, in consistency with the focus to test the gasification characteristics under a CO2 rich environment and high pressure, the results of the production of gaseous products from the gasification experiments are presented in Figures 5(a - c). From these figures, it can be generally observed that Shandong low-rank coal has a greater advantage, with regard to H2 production, than the Datong coal sample does. In addition, more CO and CH4 were produced under a specific CO2 pressure. Also, it is shown that, at normal pressure (0.1 MPa), the Shandong low-rank coal has less advantages in gasification compared with the Datong coal sample, whereas, higher pressure (0.5 - 1 MPa) appears to be more favorable to the gasification of the low rank coal. Therefore, from the foregoing observations, it could be suggested that the Shandong coal sample could be more suitable as a feedstock in a typical advanced gasification technology which is operated under CO2-rich condition and high pressure, i.e., the Integrated Gasification Combined Cycle (IGCC) technology.
3.3 Thermogravimetric characteristics of shandong (SD) low rank coal
The thermogravimetric study of coal is a well-known method for understanding the change in structural features of coal during combustion (Arenillas et al., 2004; Diaz-Faes, Barriocanal, Diez, & Alvarez, 2007; Jayaraman et al., 2015; Ren et al., 2014). The thermogravimetric (TG) and differential thermal analysis (DTA) of the SD low rank coal is presented in Figure 6. It shows that there is a small, but appreciable, weight loss within the first 25 min of combustion corresponding to the temperatures of 25 to 317 oC. The loss in weight of the coal becomes significantly rapid, from over 22 min until around 55 min of combustion (corresponding to the temperatures above 317 and 495 oC). Moreover, the change in weight loss after 55 min became negligible until after 80 min. This shows, in other words, that despite increasing the temperature from 495 to 800 oC, the weight loss remains very negligible. This characteristic behavior suggests that the combustion of the Shandong low rank coal at the low heating rate of 10 oC/min could have probably reached the climax around the temperature of 495 oC, resulting in tar formation.
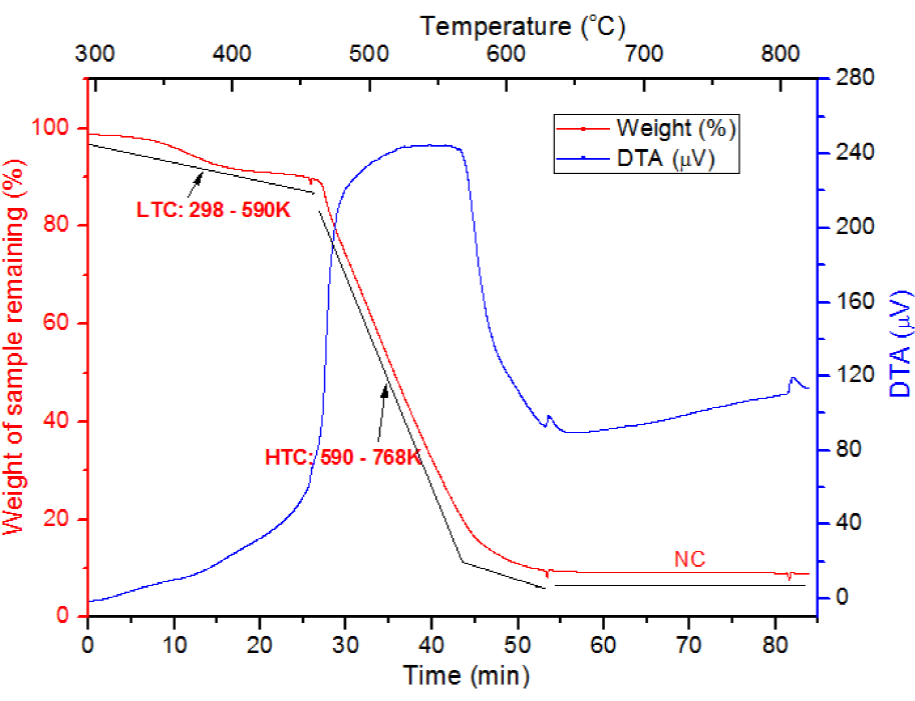
Fig. 6 Thermogravimetric and differential termal analysis (TG-DTA) profiles of Shandong low Rank coal
Similarly, from this figure, the corresponding DTG profile increases with time as earlier described for the weight loss. The highest observable peak (244 μV) is around 387 oC and 42 min combustion time at the heating rate of 10 oC/min. This behavior, as observed from the characteristic weight loss, is due to loss of volatile component of the coal around the temperature range. However, the value was observed to rapidly decrease afterwards, with negligible peaks around 532 oC. In summary, the information therefore clearly indicates that there are two main active combustion zones. The low temperature combustion (LTC) region (25 - 325 oC) and high temperature combustion (HTC) region (325 - 495 oC). Very negligible combustion activity susceptibly occurs at a temperature above 495 - 800 oC, which can be referred to as the non-active combustion region (NC).
3.4 Simulation studies: validation of the gasification model
The gasification simulation model built using the CMG STARS was validated before the commencement of the simulation to determine the best conditions for the gasification of the low rank coal under a CO2-rich condition, high pressure and rapid heating rate. This was done by setting the model parameters at the same value as the experimental environment.
As presented in Figure 7(a - c), the results of the simulation are compared with the experimental data from the gasification of the Shandong (SD) low rank coal. From these figures, the suitability of the developed CMG STARS model to simulate the gasification process under typical conditions employed in the gasification experimental studies can be clearly observed (correlation coefficient, R2 = 0.96).

Fig. 7 (a - c) Experimental and simulated results for gaseous products from gasification of SD coal.
3.4.1 Simulation of effective conditions for gasification: heating rate, CO 2 concentration, and gasification pressure
The gasification simulation data at different conditions are presented in Figure 8(a - f). Figures 8(a and b) show the simulation results on the effects of heating rate ranging from 12.5 - 50 J/s (the pressure is fixed at 0.1 MPa, with the CO2 concentration of 100% and maximum temperature of 1000 oC) on the production of gasification products (CH4, CO and H2 gases). Generally, the figures show that gas production increased with increasing the heating rate. At the heating rate of 12.5 J/s, about 1 ml of CH4, 7 ml of CO, and 0.09 ml of H2 gases were produced. At the heating rate of 35.7 J/s, the gaseous products increased to 1.8 ml, 9.8 ml, and 0.1 ml for CH4, CO, and H2 gases, respectively. In addition, from the figures, it is obvious that the heating rates at 12.5 J/s and 25 J/s are not enough for gasification, and this shows that low heating rate can decrease the gasification efficiency under the conditions presently investigated. As earlier observed in the thermal decomposition behavior of the low rank coal sample, this could be connected with incomplete gasification as certain temperature was reached, and tar was formed as reported by Fushimi et al. (2003). Moreover, it was also observed that the production gas was not increased despite the rise in heating rate to 50 J/s. This information indicates that the combustion was already completed before this heating rate. It can therefore be concluded that 37.5J/s heating rate could be effective in the gasification at the typical conditions.

Fig. 8 (a - f) Gasification simulation results for gas production at: (a and b) different heating rates, (c and d) different CO2 concentrations, and (e and f) different pressures.
Furthermore, the simulation results to study the effects of CO2 concentration on the production of CH4, CO and H2 gases at the fixed pressure of 0.1 MPa and heating rate of 37.5 J/s are presented in Figures 8(c and d). The figures clearly show that the production of CO increased appreciably from 0.4 to 1 ml as the CO2 concentration increased from 0 to 100%. In comparison, a smaller increase in the concentrations of CH4 and H2 was observed as the CO2 concentration increased. CH4 was observed to increase from 0.28 - 0.33 ml, while H2 increased from 0.04 to 0.07 ml. This might be due to the fact that the CO2 content had a great effect on the reaction balance, and more CO2 in the vessel would lead to more CO production.
Finally, the simulation results on the effects of pressure on the production of CH4, CO and H2 gases at the determined 37.5 J/s heating rate and 100% CO2 concentration are shown in Figures 7(e and f). In Figure 7(e), it can be observed that the concentration of CO increased from 1.3 to 5 ml because the pressure increased from 0.1 - 0.5 MPa. The maximum production of 7ml was reached at 1 MPa, while the value of CO production decreased to 7 ml at the pressure of 1.1 MPa. In addition, it can be observed that the cumulative CH4 production increased from 0.3 - 1 ml at the pressure of 0.5 MPa, with the maximum concentration of 1.4ml at the pressure of 1 MPa. The production decreased to 0.9 ml at the pressure of 1.1 MPa. In Figure 7(f), it can be observed that the cumulative H2 production due to pressure increased. In this case, there was a small increase in H2 production as the pressure increased from 0.1 - 0.5 MPa (0.07 - 0.09 ml). At the pressure of 1 MPa, only 0.1 ml was produced, while the value decreased to 0.08 ml at the pressure of 1.1 MPa. Moreover, these results show that the pressure had a great influence on the production of the gases, and it can be inferred that the pressure range from 0.5 - 1 MPa would be effective for the gasification of the low rank coal under a typical environment considered in the present investigation.
4. Conclusion
The primary aim of this investigation is to study the gasification characteristics of Shandong low rank coal under a CO2-rich condition, rapid heating rate, and high pressure. For this purpose, gasification studies of the coal sample and thermogravimetric analysis (TG-DTA) have been performed. The simulation model to determine the effective conditions for gasification of the Shandong low rank coal sample at high heating rate, the CO2-rich condition and high pressure were built using the data from the experimental gasification studies and the kinetic parameters obtained from the TG-DTA characteristics of the coal sample. The results have been summarized as follows:
The Shandong (SD) coal sample showed higher production of gaseous products (CH4, CO, and H2) in a CO2-rich environment and high pressure conditions compared with the Datong (DT) coal sample from the gasification experiments.
The analysis of the kinetics of combustion of the SD coal sample showed that (i) at low temperature (25 - 317 oC) combustion region, the pre-exponential factor (A) was 26 min-1. This increased to 1.18E+20 min-1 at the high temperature (317 - 495 oC) combustion region. The activation energies (E a ), at these regions, were 28 and 235 KJ/mol, respectively.
The gasification model, which was built using the CMG STARS, was found to be suitable for predicting the gasification characteristics under the experimental conditions conducted. Moreover, from the simulation results, it was found that the effective gasification conditions resulting in the higher production of gaseous products (CH4, CO, and H2 gases) from the gasification of the Shandong low rank coal was 100% CO2 concentration, 37.5 J/s heating rate, at the pressure range of 0.5 - 1 MPa.