1. Introduction
In the midst of growth of global economy and population, industries have been generating enormous amount of solid wastes like agricultural wastes and manufacturing by-products due to the increasing demand of goods by consumers. This waste problem has been a continuous issue, not only for the environmentalists but also for the society as a whole. To date, the safe disposal of large amounts of waste is still a major concern as it may have disastrous effects on the environment and on people in the near future. Hence, multiple research has been actively conducted to explore alternative waste management strategies to minimize the environmental pollution caused by these wastes. One of them includes reutilizing the generated industrial wastes as valuable and profitable products which can be used in some notable applications. For instance, the large amount of agricultural wastes can be utilized as the source of bio-based silica by extraction method.
Malaysia has become one of the biggest producers and exporters of palm oil and palm oil products worldwide whereby it currently accounts for 28% of the global palm oil production and 33% of world export (Malaysian Palm Oil Council [MPOC], 2020). Being the key contributor to Malaysia’s economy, the oil palm plantation and palm oil processing sectors or milling plants amply generated an overall surplus of palm oil byproducts (Osman & Sapawe, 2020a), thus significantly contributes to environmental degradation if proper waste management is not practiced (Aziz & Hanafiah, 2017). The manufacturing processes generate large quantities of empty fruit bunch (EFB), palm kernel shell (PKS), decanter cake (DC) and palm oil mill effluent (POME) on the output side. The solid wastes from palm oil mill industries in Malaysia have been increasing annually at a rate of 4 million tons per year (Ghani et al., 2019). In typical palm oil mill, only 30% of the total fresh fruit bunches (FFB) are turned into valuable crude palm oil while the remaining 70% are merely wastes in the form of EFB, PKS, fibers and POME (Zafar, 2020). These wastes are traditionally used as solid fuels to generate electricity from steam in steam boilers and turbines (in-house energy generation), often burnt causing air pollution, and dumped recklessly, or discarded in disposal waste ponds, which then resulted in the leaching of contaminants, as well as groundwater and soil pollutions, and subsequently, caused the release of methane gas to the atmosphere (Zafar, 2020). It was also studied that the combustion of wastes as boiler fuel by palm oil mill produces 5% of palm ash and because of the limited uses of this ash, the wastes are currently disposed to landfills which leads to detrimental environmental problems (Faizul et al., 2014).
Silica, or chemically known as silicon dioxide (SiO2), is one of the valuable inorganic compounds that exists abundantly and naturally as quartz, sand or flint in various forms such as gel, crystalline and amorphous forms (Faizul et al., 2014). It is largely used as moisture absorbents, refrigerant in drying, glass insulators, packaging desiccants (Abdul Samat et al., 2018) to produce ceramic products and electronic components, concrete additives (Faizul et al., 2014) and many others. However, the traditional method of manufacturing pure silica by smelting quartz sand with sodium carbonate consumes extensive amount of energy at an operating temperature of 1300°C (Abdullah & Sulaiman, 2013; Abdul Samat et al., 2018; Faizul et al., 2014; Sapawe et al., 2018). It is an energy intensive process that can deteriorate the environment as much heat is produced and lost throughout the process.
Previous studies have shown that agricultural wastes can also contain siliceous material such as in palm ash, rice (Faizul et al., 2014), sugarcane bagasse, corn cob, bamboo leaves (Sapawe et al., 2018), and oil palm frond ash (Osman & Sapawe, 2020a). There is extensive research conducted to explore the methods for extracting bio-based silica from agricultural wastes (Faizul et al., 2014). There are three main methods for producing silica from agricultural wastes which are via chemical, heat and microbial treatments (Permatasari et al., 2016). Agricultural wastes which are used as alternative silica source will not only provide advantage in the form of inexpensive raw material, but it can also help to minimize waste production. The research on silica synthesis from agricultural waste is gaining more popularity nowadays as it can provide an alternative to the conventional commercial silica precursor such as tetraethyl orthosilicate (TEOS) and tetramethyl orthosilicate (TMOS). The aim is to produce potential precursor that is possibly economically and environmentally friendly as compared to conventional silica produced from sources such as sand and feldspar (Sapawe et al., 2018). Typical silica which come from conventional sources are expensive which opens avenue for possible economical silica precursors from waste materials such as agricultural wastes (Sapawe et al., 2018). Although their silica content and production may not be as high as the silica manufactured from quartz or sand, they are still valuable to support the silica demand in many industries (Faizul et al., 2014). Therefore, aligned with the effort to maximize the use of wastes, there is a large potential to extract bio-based silica from these palm oil wastes, i.e., EFB, PKS and DC in Malaysia.
Although the characterization of silica end products has been extensively researched, there are limited studies on the relationship of the varying calcination temperatures and the physical and microstructural properties of the calcined ash samples prior to silica extraction method e.g. sol-gel or acid leaching. Therefore, this paper fundamentally discusses the effects of different calcination temperatures (heat treatment), ranging from 400°C to 800°C, on the physical and microstructural properties of the palm oil mill wastes, prior to exploring the silica extraction process. These temperatures are tested as they are apparently lower than the temperature or energy required in silica manufacturing from natural quartz, yet adequate to produce silica and support its industrial demand. The temperature effects are analyzed based on physical weight loss, color analysis, BET, SEM and FTIR.
2.1. Raw materials
Sarawak palm oil wastes known as empty fruit bunch (EFB), palm kernel shell (PKS) and decanter cake (DC) were employed as the raw material. The wastes were collected locally from FELCRA Jaya Palm Oil Mill in Kota Samarahan, Sarawak, Malaysia.
2.2. Sample preparation
There are three main stages of sample preparation prior to their physical analysis and morphological characterization; 1) acid washing or pre-treatment, 2) oven drying and 3) calcination thermal treatment. These stages are briefly summarized in Figure 1.
In acid washing, 20g of sample were soaked in 60ml of distilled water and washed with 1M of citric acid to adjust the pH to 1. The acid treatment was conducted to leach out impurities like the metal compounds that would increase the purity of silica, especially for the next phase of silica extraction process. The mixtures were stirred for 2 hours until uniform pH was achieved, and most impurities were leached into the solution. The mixtures were then filtered using filter paper and the residual wastes were washed thoroughly using three batches of 100ml distilled water. The residues were then dried for 24 hours in an oven operating at 60°C to remove moisture and to avoid fungal attack (Nordin et al., 2016).
The dried and acid-treated palm oil mill waste samples were then calcined in a furnace for 6 hours at varying temperatures, i.e., from 400°C to 800°C at intervals of 100°C. The ash obtained was then grounded for 30 minutes and sieved to obtain consistent particle sizes of 20 to 30 microns. The effects of the different calcination temperatures on the samples were then observed based on several basic physical and microstructural properties such as weight loss, color analysis, BET, SEM and FTIR.
2.3.1. Weight loss analysis
A weight loss analysis was conducted to observe how much impurities were removed from each batch of waste sample after the acid washing and calcination (heat treatment) process, thus subsequently indicating the potential amount of non-combustible silica remaining in the waste samples. It is known that these chemical and heat treatments can reduce the content of metal impurities and carbonaceous substances present in the samples. Weight loss is evaluated using Eq. 1
where W1 and W2 refer to the weights of the samples before and after calcination, respectively.
2.3.2. Color analysis
The colors of all the ash samples produced after 6 hours of thermal treatment in a furnace were analyzed and compared by both the naked eye and whiteness quantification using Eq. 2. Prior to the use of Eq. 2, Matlab software was used to extract the pixel data and HSV color spaces from the image input and produce values of L*, a*, and b*. It is often known that the higher the value of whiteness of the ash samples (WI), the more complete the combustion takes place, thus leaving high relative amount of non-combustible silica in the waste samples.
2.3.3. Characterization analysis
Every batch of calcined ash samples, i.e., EFB ash, PKS ash, and DC ash, produced at temperatures of 400°C, 500°C, 600°C, 700°C, and 800°C for 6 hours, were characterized using Brunauer-Emmet-Teller (BET), Scanning Electron Microscopy (SEM) and Fourier Transform Infra-Red (FTIR) Spectroscopy using Quantachrome (Model: ASIQC0000-3) and Shimadzu FTIR Spectrometer (Model: IRAFFINITY-1), respectively.
3. Results and discussion
3.1. Weight loss analysis
The weight loss of palm oil wastes after acid washing and 6 hours of heat treatment at varying calcination temperatures were recorded and illustrated in Figure 2. The initial masses of the wastes were weighed at 20g before calcination process.
Comparing all the palm oil waste samples, EFB records the highest weight loss at all calcination temperatures, followed by PKS and DC. 20g initial weight of EFB sample drastically drops to less than 1g at temperatures above 400°C with weight loss as high as 96.1% at 400°C. It is also observed that almost all EFB waste (99%) were combusted off at 800°C, leaving negligible amount of non-combustible ash. For PKS and DC, slightly more samples of approximately 5.48g and 7.88g, respectively, remained at 400°C. DC resulted in the lowest weight loss of 84% at 800°C, which is about 11% lower than PKS. By relation, all weights of EFB, PKS and DC samples decreased consistently above 400°C according to the best-fit polynomial relationship of Eqs. 3, 4 and 5, respectively.
The trend in Figure 2 also generally illustrates that the weight loss of all samples has positive correlation with the increase of calcination temperature, that is, the higher the heating temperature, the greater the amount of sample weight loss. According to Bakar et al. (2016), the weight loss in the samples was due to the amount of evaporation of available organic groups, water formed by reactions, and volatile compounds formed. Among the reasons for this, the decomposition of hemicellulose and lignin found in crops can be mentioned. This therefore indicates that the greater the weight loss, the greater the amount of combustible and evaporative materials present in the sample, in relation to the amount of non-combustible element like silica. In this case, DC has depicted the lower weight loss of 84% per 20g of sample when calcined at 800°C, thus demonstrating that it contained more bio-silica in comparison to other materials within its sample, than PKS and EFB. These results are also supported by another research study that similarly reported that the amount of silica extractable from PKS was slightly greater than EFB (Abdul Samat et al., 2018).
3.2. Color analysis
Figure 3 presents the images of all samples calcined at different temperatures between 400°C and 800°C. It is observable that at high calcination temperature, more white ash samples were produced.
A quantitative color analysis was conducted by evaluating the whiteness of the samples using MATLAB software whereby RGB color space was extracted for each of the samples and converted into lab color space. Figure 4 displays the calculated whiteness of all ash samples produced. It is generally observed that the whiteness value for all types of palm oil wastes increase over the increase in calcination temperature, with the highest whiteness achieved at 800°C, i.e,. at 85.27, 50.49 and 72.18 for EFB, PKS and DC. respectively. As whiteness of the ash samples is associated to the amount of pure non-combustible silica (Wardhani et al., 2017), EFB has therefore shown to contain the purest silica when calcined at 800°C compared to PKS and DC. Besides, amongst all waste samples, EFB400 records the lowest whiteness value of 0.31, which depicts that it contains relatively higher amount of non-silica materials. This value, however, increases exponentially to 85.27 as portrayed by EFB800. This is consistent with its considerable weight loss result, whereby almost 99% of its combustible materials are evaporated off at 800°C, leaving only traces of pure silica.
Similar positive trend is as well observed on both DC and PKS samples whereby the whiteness values increase by 67.30, i.e,. from 4.88 (DC400) to 72.18 (DC800), and by 47.13, i.e., from 3.36 (PKS400) to 50.49 (PKS800), respectively. The relative amount of pure silica in DC800 therefore, ranks the second before PKS.
The presence of metal ion impurities and unburned carbon in biomass samples has adverse effect on the product color and purity (Ghorbani et al., 2015), incomplete combustion at low temperature produces black or grey ash which is detected to still contain inorganic impurities and unburned carbon amounts. On contrary, when complete combustion is operated, white-colored ashes shall be produced because of the effective removals of carbon and metallic impurities (Della et al., 2002), thus producing high purity of silica-ash.
3.3. BET analysis
The values of BET specific surface area (SBET) tabulated in Table 1 were those obtained for EFB, PKS, and DC ashes produced at 500°C and 800°C. They were calculated by using Brunauer-Emmett-Teller (BET) equation. As shown, all samples exhibited an obvious increment of 1.10% to 4.21% surface area. The comparison temperatures chosen were 500°C and 800°C because of the significant changes occurring at these temperatures. The highest surface area was achieved by PKS (4.21%) as compared to EFB and DC which are only at 2.82% and 1.10% respectively. This might be due to the initial preparation of samples, i.e., pretreatment with citric acid that caused leaching of impurities thus exposing more surface area within the sample, as well as the possible reaction with trapped acid during high temperature calcination process.
Table 1 SBET of EFB, PKS and DC ash produced at temperatures 500°C and 800°C.
Samples | BET Surface Area (SBET) (m2/g) | Surface Area Increase (%) |
EFB500 | 3.956 | 2.82 |
EFB800 | 15.100 | |
PKS500 | 3.853 | 4.21 |
PKS800 | 20.087 | |
DC500 | 4.520 | 1.10 |
DC800 | 9.492 |
The N2 adsorption isotherms for EFB, PKS and DC at 500°C and 800°C, respectively, are shown in Figure 5. PKS500 showed a rather flat isotherm, extended up to P/Po = 0.400, as compared to the rest of the samples. EFB, PKS and DC performed better at 800°C than at 500°C. This is because, the high temperature causes the destruction of walls between two adjacent pores, enhances and widens the existing pores, and thus creating new porosities with higher surface area for greater adsorption capability onto the materials (Kumar & Jena, 2016; Tan et al., 2008).
The physical properties of the ash are mostly affected by pyrolysis condition, particularly temperature, such that, as the pyrolysis temperature increases, the surface area and pore volume subsequently increase (Figueiredo et al., 2018; Larichev et al., 2015) due to destruction of pore structure of the ash. As claimed by Larichev et al. (2015), the density and residual content of silica in the sample also increase with the increase in temperature, which supports the results displayed in Table 1.
3.4. SEM analysis
Figure 6 to Figure 8 depict the SEM images of EFB, PKS and DC at various calcination temperatures and scanned at magnification of ×1000. From the SEM images, EFB, PKS, and DC particles are observed to have a porous and spongy texture with irregular and angular shapes, which is in agreement with Yahya et al. (2010). As also mentioned by Quercia et al. (2013), the silica has an irregular shape, grouped into spherical clusters. The irregular shape which is assumed to be silica can be detected in all the SEM images. To prove the presence of silica, a FTIR analysis was conducted and confirmed with the existence of IR peaks. This kind of shape was also detected by Wan Chik et al. (2011) . The reason for the irregular shape was typically the agglomeration of silica. As the calcination temperatures were increased, almost all the particles are observed as smaller particles and more agglomeration can be seen. It was mainly due to the mineral appearance in the crystal form at higher temperature as the particles became more brittle. Most irregular shape and crystalline structure of silica can be observed in the images of sample burn at high temperature of 800°C. The appearance of a crystalline structure also indicated that the samples contained a smaller amount of unburned particles such as carbon. In addition, it can be observed that the ash produced at the temperature of 800°C was not highly bonded with other impurities. The impurities were assumed to be totally removed at the high temperature of 800°C as shown in Figure 6(a), Figure 7(a) and Figure 8(a). It can be concluded that EFB, PKS, and DC were combusted at high temperature producing a high amount of pure silica.
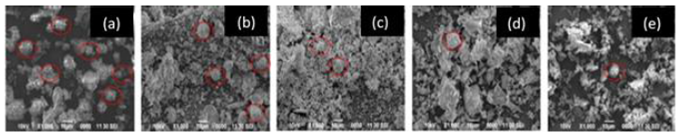
Figure 6 SEM images of empty fruit bunch (EFB) ash at various calcination temperatures: (a) EFB800, (b) EFB700, (c) EFB600, (d) EFB500, (e) EFB400. DC.
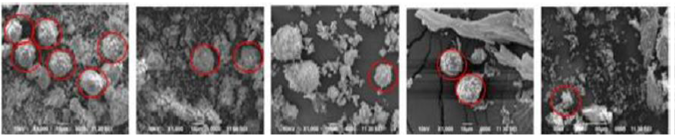
Figure 7 SEM images of palm kernel shell (PKS) ash at various calcination temperatures: (a) PKS800, (b) PKS700, (c) PKS600, (d) PKS500, (e) PKS400.
3.5. FTIR spectroscopy
The FTIR spectra obtained for the samples of EFB, PKS and DC at various calcination temperatures are illustrated in Figure 9. FTIR was used to observe and identify the major functional groups exist within the samples. The potential of these samples as the source of bio-silica, therefore, highly depends on the availability of silica chemical groups in the samples. As summarized in Table 2, there are 5 dominant peaks which are associated to silica bonding, carbon-hydrogen interaction and hydroxyl groups evident in EFB, PKS and DC wastes.
Table 2 FTIR peak assignments for EFB, PKS and DC.
Wavelength (cm-1) | Assignment |
746 - 751, ~880 | Si-C bond |
771 - 795 | Symmetric stretching of Si-O-Si |
1026 - 1046 | Asymmetric stretching of Si-O-Si, vibration of Si-O bond |
1409 - 1460 | In-plane C=H bond |
1649 - 1702 | OH bending vibrations of water (H2O) and hydroxyl (Si-OH) |
The most prominent IR absorption band is located between 1026cm-1 and 1046cm-1 whereby the peaks can be clearly seen in all samples calcined at a minimum temperature of 500°C. They are attributed to the asymmetric Si-O-Si stretching with stretching vibration of Si-O bond. Bands located between 1000cm-1 and 1200cm-1 commonly observe antisymmetric bonds which represent the existence of silica in the intended materials (Portaccio et al., 2011). This is as well supported by much research which has reported nearly close absorbance bands assigned as Si-O-Si chain stretching, i.e., 1064cm-1 by Portaccio et al. (2011), 1086cm-1 by Awadh and Yaseen (2019), and between 1040cm-1 and 1100cm-1 by Osman and Sapawe (2020b). From the spectra, observable peaks of Si-O-Si do not arise at lower temperatures as indicated by the curves of EFB400, PKS400 and DC400 around the said band range. It is hence shown that Si-O-Si content is not noticeable in samples calcined lower than 500°C. Besides, consistent locations of peaks between 1026cm-1 and 1046cm-1 for calcination temperatures beyond 400°C confirms that silica is present in EFB, PKS and DC wastes.
Another visible bands which are typically shown by the samples are located within 781cm-1 to 795cm-1, 786cm-1 to 795cm-1, and 771cm-1 to 785cm-1 for EFB, PKS and DC samples, respectively. This corresponds to the symmetric stretching of Si-O-Si chain, thus again, depicting the presence of silica compounds in the samples. Portaccio et al. (2011), Yuvakkumar et al. (2014) and Awadh and Yaseen (2019) have observed respective peak bands of 787cm-1 (Portaccio et al., 2011), 795cm-1 (Yuvakkumar et al., 2014), and 790cm-1 (Awadh & Yaseen, 2019) related to symmetrical Si-O-Si vibrations. Similar to asymmetric Si-O-Si FTIR spectra, these bands are only obvious for samples exposed to high temperatures, no less than 500°C.
As obtained by Li et al. (2020), typical peaks interpreted as Si-C vibrations are viewed at bands near 756cm-1, 842cm-1 and 1255cm-1. In Figure 9(a), absorption at 750cm-1 is observed on EFB400 sample. However, it is no longer seen in samples treated at 500°C and beyond, which hence indicates that combustible carbons of Si-C may have been effectively removed from the samples as temperature increases. Similar absorption is obtained at 746cm-1 on FTIR spectrum of PKS400, but none is detected for DC samples. Moreover, it is also evident that Si-C bands located near 840cm-1 and 1250cm-1 are not observable in all EFB samples. On contrary, several minor peaks about 880cm-1 are obvious in PKS and DC, but none near 1250cm-1 is observed. The small amount of non-combusted carbon of Si-C as detected in PKS and DC is coherent with their color analysis results whereby both samples produce lower whiteness values than EFB, especially at 700°C and 800°C. Furthermore, carbon-hydrogen (C-H) bonds, as attributed by bands between 1409cm-1 to 1460cm-1, are also noticed in PKS and DC samples. The non-combusted carbon elements, again, cause them to have darker colors than the EFB samples. Overall, these results depict that the EFB samples contain the lower amount of Si-C or C=H, while both PKS and DC are still having minimum traces of carbon even after calcined at high temperatures up to 800°C.
Besides, DC samples also portray visible peaks associated to free bending vibrations of OH of Si-OH bonds and H2O, which are generally located between 1600cm-1 and 1700cm-1 (Awadh & Yaseen, 2019). They can be viewed at bands 1686cm-1, 1649cm-1 and 1686cm-1 by DC400, DC500 and DC600 samples, respectively. The presence of this hydroxyl functional group is generally due to the rinsing of samples using distilled water as well as the introduction of carboxyl group from citric acid C6H8O7 during sample preparation. However, the peaks are no longer visible in DC700 and DC800 samples as OH groups evaporate at high temperatures. Besides, the PKS samples which are exposed to 400°C and 500°C also display peaks at the respective bands of 1697cm-1 and 1701cm-1, and the peaks get less visible near similar positions for higher temperature PKS samples. Overall, hydroxyl impurities are shown to be effectively removed with the increase in the calcination temperature, thus producing higher purity of silica ash samples.
In general, the FTIR analysis has shown that silica content remains within all samples, even after exposed to high calcination temperatures up to 800°C. Besides, as shown by the more flattened peaks of impurities at 800°C, the purity of silica ash samples (EFB, PKS and DC) improves along with the increase in temperature as most impurities such as carbon elements and hydroxyl groups are removed at higher calcination temperatures.
4. Conclusions
Current research mainly focused on investigating the biomass wastes from palm oil production, which comprised of EFB, PKS and DC that underwent calcination process to produce potential bio-silica. As expected, it was discovered that all samples had favorably produced a relatively high amount of silica. Particularly, for this research, in order to exhibit silica, the calcination process at temperature of 800°C ended up being an optimum temperature. All the samples evidently observed the presence of silica from FTIR spectra that located within the range of 1026cm-1 and 1046cm-1. The exhibited silica was identified as asymmetric Si-O-Si stretching with the stretching vibration of Si-O bond. In addition, the samples were highly visible as white ash, especially for EFB samples.
Mostly, this was due to an effective removal of carbon and metallic impurities that led to the high purity of silica-ash. The purity of silica ash samples (EFB, PKS and DC) improves along with the increase in temperature as most impurities such as carbon elements and hydroxyl groups are removed at higher calcination temperature. The weights of all samples were distinctly decreased at temperature above 400°C. DC sample depicted the lower weight loss of 84% per 20g of sample when calcined at 800°C, therefore more bio-silica in comparison to other materials within its sample. Meanwhile, PKS sample reported to demonstrate high surface area which reflected the high porosity presence. In conclusion, the biomass wastes, i.e., EFB, PKS, and DC had positively presented a potential contribution towards the production of bio-silica. The research will be further investigated as it is a promising research as an initial step to go from waste to wealth concept.