1. Introduction
Pathological manifestations are present in most buildings to a greater or lesser extent, varying their appearance period and requiring diagnosis and repair, or sometimes in a more complex way, requiring a personalized analysis (Ferreira & Lobão, 2018). However, even when they directly interfere in a building useful life and performance, -generating discomfort and risk both for people who directly use the building and passers-by in surroundings-, analysis and treatment of pathological manifestations is not a priority (Bauer et al., 2011; Viégas, 2015). Many times this structure does not obtain required attention regarding design, execution and maintenance. This is a fact that increases susceptibility about development and aggravation of pathological manifestations (Silva, 2007).
Considering this, investigation and monitoring process for buildings is essential because such procedures enable monitoring their behavior throughout their use in an enterprise, thus gathering information that enable monitoring and detecting failures when sent to obtain analysis and decision models (Agostinho, 2012). In that sense, destructive tests applied to materials, components or building systems become undesirable when it comes to problem diagnosis in the context of in-use buildings. In fact, development of non-destructive techniques intended to diagnose building deterioration, has generally been study subject for many researches (Freitas et al., 2014). Since then, using infrared thermography and Unmanned Aerial Vehicles (UAVs) in building inspection processes has been explored and spread out in society (Nascimento, 2014; Ellenberg et al., 2016; Entrop & Vasenev, 2017).
Thus, infrared thermography is a non-destructive technique involving remote sensing images used to detect flaws in electrical equipment, as well as changes in different parts of a building such as roof, structural systems, masonry sealing systems and coatings. One of these changes refers to detection of excessive humidity and temperature, responsible for damaging materials, with consequences on human health (Cortizo, 2007; Lerma et al., 2011; Freitas et al., 2014). Despite infrared thermography technique has been widely spread in European countries, thanks to historical collection, in Brazil its use is relatively incipient, either due to analysis equipment cost or difficulty on practical application (Cortizo et al., 2008 ).
Simultaneously, UAV usage has been subject to studies regarding building inspection to verify performance conditions and determine preventive and corrective measures that might be required, due to inherent complexity (height, size, access difficulties and exposure conditions) (Witczuk et al., 2017). UAVs may reduce time in these monitoring operations, and also assist in other inspection processes involving human life risk (Álvarez et al., 2016). In this context, the current article presents application of an infrared camera integrated with Unmanned Aerial Vehicles (UAV) as a tool for building inspection and monitoring to define procedural factors (influencing factors to achieve accurate thermograms used to identify pathological manifestations), in addition to advantages and limitations of this technology.
2. Bibliographical review
2.1 Infrared Thermography
Infrared thermography is a predictive tool used in early diagnosis of failures and other problems (performance analysis study to predict and specify possible anomalies, assisting in preventive maintenance). Results are presented instantly, during inspection, in form of thermal images or thermograms, which represent surface temperature distribution for an observed object and, as such, recorded for subsequent action purposes by interested parties and archiving (ITC, 2014).
Infrared thermography systems capture thermal radiation, represented in an electromagnetic spectrum, -by the fact that all bodies are at a temperature above absolute zero and emit radiation that is converted into a thermogram which has a polychromatic (color) or monochromatic (gray) scale. Infrared radiation (IR) was first discovered by William Herschel in 1800, and thermoelectric effect was discovered by Thomas Johann Seebeck in 1821. This effect is a direct conversion between temperature difference and electrical voltage and vice versa, being this effect the basis for thermal camera operation (Mistry, 2009; Viégas, 2015). Thermal radiation emitted by an object and captured by a thermal camera is given by Stefan-Boltzmann's law (1).
Where E is the radiation emitted by the object (W/m²), q is the degree of energy emission (W), A is the area of an emitting surface (m²), T is the absolute temperature (K), σ is the Stefan-Boltzmann constant of 5.676x10-8 Wm-2K-4, and ε is the emissivity of an emitting surface, whose value is between 0 and 1, and indicates how close a surface is to the behavior of a black body, which would be an ideal surface where radiation rate would be maximum, so 𝜀=1. (Çengel and Ghajar, 2012).
Additionally, this technique may be classified as active or passive according to thermal overload being used. In active thermography, an external stimulus is required to generate relevant temperature differences. Different techniques may be employed to cause a heat flow in the study subject, each with its own characteristics and limitations. The choice on the type of thermal stimulus depends on characteristics of the object to be tested and the type of information to be researched (Batista, 2019).
On the other hand, using passive thermography where no artificial stimulation is used, involves a natural temperature difference that must be present between the study subject and the medium where it is inserted, which is frequently at a higher temperature. A passive method analysis relies on natural conditions for a studied structure and its surroundings, sun heat being a determining factor (Cortizo, 2007). Therefore, as shown in Figure 1, thermographic cameras capture infrared energy emitted by objects to convert this energy into an electrical signal and, finally, into a visible image, in which each level of energy is represented in a color scale (Meola & Carlomagno, 2004).
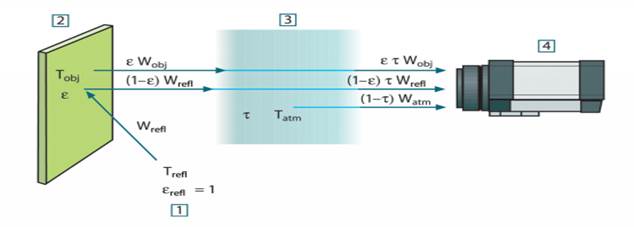
Figure 1 Schematic representation of general thermographic measurement location. 1) adjacent environment, 2) object, 3) atmosphere, 4) camera. Tobj: object temperature, Trefl: reflected temperature, Tatm: atmospheric temperature. Wobj: radiation power emitted by the object, Wrefl: radiation power emitted by surrounding environment, Watm: radiation power emitted by atmosphere (Caldeira & Padaratz, 2015).
Thus, this technique implemented in buildings may be used to evaluate comfort on floor covering (Barreira et al., 2013), detect insulation defects, air leaks (Ocaña et al., 2004) moisture problems (roof damage, moisture on walls), thermal bridges (Asdrubali et al, 2012), and inspect HVAC systems (Heating, Ventilating and Air Conditioning), construction details (Cerdeira et al., 2011; Barreira et al., 2013) and also in building inspection (Brique, 2016), as shown in Figure 2.
According to variables highlighted in Table 1, the higher the thermal resolution (pixels) in a camera, the more likely to inspect larger areas with greater precision. Therefore, when using thermal cameras integrated with UAV, they must have the best resolution possible. Furthermore, the IFOV (Instantaneous Field of View) value and the lens opening angle are one of the main limitations in studies involving the analysis of buildings. The higher these parameters, the lower thermogram resolutions and study accuracy will be (Andrade et al., 2019). In addition, it should be noted that the inspection is limited only to a passive application of infrared thermography, which would mean that inspection to the structure would not be possible every day, or that it would be restricted to locally determined schedules.
Table 1 Key variables related to a thermographic camera (Andrade et al., 2019)
PIXEL CAMERA RESOLUTION | IFOV (Instantaneus Field of View) | LENS OPENING ANGLE |
---|---|---|
60 x 60, 120 x 120, 240 x 380, 320 x 240, 640 x 480. | The value varies between 0.6 and 3.7 mRad, using the equipment lens. | The most common lenses are 15 and 25 degrees but can vary between 7 and 80 degrees. |
2.2 UAVs
According to ANAC (National Civil Aviation Agency, 2017), unmanned aerial vehicles (UAVs) are any unmanned aircraft that can be remotely or automatically driven. These aircrafts are remotely or automatically flown using predefined coordinates. It is a technology on the rise that is being used in several areas every day (Nascimento, 2014). UAVs were first developed in the 1950s and were exclusively intended for military purposes. Different projects started in several countries with the purpose of producing vehicles capable of performing missions without a pilot on board in order to avoid further losses (Agostinho, 2012). Over time, technology began to get disclosed, and its first use for a non-military purpose took place in 1986, when forest fires were monitored in Montana, United States (Agostinho, 2012). In this sense, increasing UAV usage is due to its low cost, agile processing collection, easy aircraft maneuvering, and efficient image capture system (Seibert & Teizer, 2014).
Besides, UAVs are effective tools to perform remote sensing procedures, including its capability for reaching places that are difficult to access as the main reason to be used, as well as a range of applicable sensors that can be incorporated such as an infrared camera, light detection and distance sensors (LIDAR, Light Detection And Ranging) (Freimuth & König, 2018).
Currently, two types of UAVs, whose basic difference is their aerodynamic system such as a rotation or fixed wing, are available in the market. The first aircrafts are similar to a helicopter or multirotor, a compact aircraft involving easy operation and low cost. On the other hand, fixed-winged aircrafts include different sizes according to functionality (Jorge & Inamasu, 2014; Melo & Costa, 2015).
Table 2 UAV Classification (Bento, 2008).
CATEGORY | ACRONYM | RANGE [km] | FLIGHT ALTITUDE [m] | BATTERY AUTONOMY [h] | WEIGHT [kg] |
---|---|---|---|---|---|
Micro | μ (micro) | > 10 | 250 | 1 | >5 |
Mini | Mini | > 10 | 150 – 3000 | > 2 | 150 |
Close Range | CR | 10 – 30 | 3000 | 2 – 4 | 150 |
Short Range | SR | 30 – 70 | 3000 | 3 – 6 | 200 |
Medium Range | MR | 70 – 200 | 5000 | 6 – 10 | 1250 |
Medium Range Endurance | MRE | >500 | 8000 | 10 – 18 | 1250 |
Low Altitude Deep Penetration | LADP | >250 | 50 – 9000 | 0,5 – 1 | 350 |
Low Altitude Long Endurance | LALE | >500 | 3000 | >24 | <30 |
Medium Altitude Long Endurance | MALE | >500 | 14000 | 24 – 48 | 1500 |
Table 2 shows that UAVs used in building inspection process in general have a weight below 150 kg. The flight range, a dominant factor for flight protocol development and efficiency in building monitoring, is below two hours.
2.3 Thermography integrated with UAV
Although thermography and UAVs are subject to different recent investigations, an integrated study of both is still incipient. Analyzing benefits related to these two topics motivates a combination of their functionalities to obtain mutual benefits (Entrop & Vasenev, 2017). A thermal camera integrated with an UAV is an important tool to evaluate large areas in an automated way and in reduced runtime (Viana et al., 2018). Main challenges for this technology are low resolution of some thermographic cameras, regulations that limit operations involving UAV on a visual line and high dependence on climate (Witczuk et al., 2017).
In addition, heat sensors are a payload option for high resolution aerial thermal imaging. This technology enables quick and safe survey of thermal areas, often present in inaccessible or dangerous terrain (Harvey et al., 2016). These images collected by UAV are potentially critical tools in geothermal science, including geological, geochemical and geophysical surveys, study and environmental monitoring baselines, geotechnical and civil works, and as in the case of this research, an outstanding support for building inspection. Such technology may be used for mapping heat loss, and be able to gather thermal information such as heat leaks, by using an infrared camera and then processing any image obtained. Despite performing inspections, it is a less difficult process for small buildings, collecting thermal data with increasing height, especially on skyscrapers and roofs, and is a much more complex and dangerous process (Kayan et al., 2018). Aerial thermography is a technology that has been used in recent times to record thermal images without requiring access to buildings, and it is capable of reaching any difficult-access area such as a roof, while carrying an infrared camera and any other sensor (Chu et al., 2016).
Therefore, combining infrared thermography and UAVs enables optimization of maintenance tasks (Muñoz et. al., 2017), and consequently, bringing significant economic advantages (Ramírez et al., 2018). Such aspects are due to the fact that UAVs may be equipped with high-resolution cameras allowing users to obtain data in real-time. Furthermore, aerial images previously captured from another light aircraft or helicopter and their fuel cost are disadvantages that make UAVs more viable, since power source for their flight can be easily recharged (Lavars, 2015). Therefore, being equipped with a high-resolution thermographic camera, an UAV becomes an excellent tool to collect thermal information from buildings (Zhang et al., 2015). In that sense, Figure 3 shows an UAV model that is already integrated with a digital camera as well as a thermographic camera, different from other models. Removing the first camera to install the second camera is required.
3. Building inspection
Thermography implementation in inspection processes is based on existing anomalies or defects that impact thermal properties in the structure. Figure 4 shows defects interrupting heat transfer from concrete, since existing voids are filled with air or water, and due to different thermal conductivity in materials, temperature variation along the structure is verified (Rocha & Póvoas, 2017).

Figure 4 Modeled propagation of a single heat pulse in a material: (a) An energy pulse applied to the surface; (b) A heat pulse travels inside the material and finds a defect; (c) This defect partially reflects and partially transmits the pulse (Cortizo, 2007).
Additionally, infrared thermography produces a thermal image, where each color represents a surface temperature level in objects. By analyzing any image obtained by the equipment, it is possible to identify foci of humidity, anomalies, hidden elements, and other defects present (Grinzato et al., 2011). Consequently, infrared thermography enables detecting only anomalies associated with measurable modifications of thermal characteristics such as heat flow and resulting temperatures, and pathological manifestations with limited depths, i.e, near the surface (Bauer & Pavón, 2015). In civil construction, therefore, a temperature range from 1 °C to 2 °C is generally an indication of potential issues. From 4 °C on, existing body abnormality may be ascertained (Maldague & Marinetti, 1996; Cortizo et al., 2008).
Therefore, this technology enables identification of adhesion failure or absent mortar (Bauer et al., 2015), and confined moisture present in ceramic tiles (Edis et al., 2014; Bauer & Pavón, 2015), as well as existing cracks, detachment problems, and infiltrations, considering the thermal gradient verified in the thermogram (Freitas et al., 2014; Viégas, 2015; Rocha & Póvoas, 2017; Takeda & Mazer, 2018; Batista, 2019).
In the case shown in Figure 5, according to Nascimento (2014), images were obtained in the early morning, making it possible to recognize areas including cracks and infiltrations, as the weather was mild and allowed a greater difference in temperature gradient, with lighter regions being those that have a higher temperature than those that are represented in darker tones.
3.1 Advantages and disadvantages
Table 3 shows the main advantages and limitations of using a thermographic camera integrated with an UAV according to literature (Yehia et al., 2007; Agostinho, 2012; Sham et al., 2012; Jorge & Inamasu, 2014; Mavromatidis et al., 2014; Seibert and Teizer, 2014; Domingues, 2015; Melo and Costa, 2015; Pajares, 2015; Watase et al., 2015; Zhang et al., 2015; Ariwoola, 2016; Ellenberg et al., 2016; Hiasa et al., 2016; Rehman et al., 2016; Entrop & Vasenev, 2017; Muñoz et al., 2017; Witczuk et al., 2017; Freimuth & König, 2018; Ramírez et al., 2018; Andrade et al., 2019).
Table 3 shows that main advantages of using this technology are linked to optimizing inspection procedures, obtaining data in real time and in a shorter interval of time. On the other hand, limitations are related to requirements to obtain an accurate thermogram, considering favorable climatic conditions and readings made from angles and distances unable to interfere with the results.
Table 3 Advantages and limitations of using a thermal camera integrated with an UAV
VANTAGENS | LIMITATIONS |
---|---|
• Capability of reaching difficult access areas; | • Flight autonomy from 30 min to 2 h, using ˂ 150 Kg models; |
• Getting real-time data; | • Favorable weather conditions, implying both flight and surface heat emissivity; |
• Reducing operational risks; | • Subject to local regulations and restrictions for flight performances, unable to be performed in any location; |
• Increasing operator and employee safety; | • Interference in results due to reflections if used in a facility surrounded by buildings including mirrored facades; |
• Reduced inspection time that generates savings and speeding up recovery planning for a structure; | • Changes in scanning obtained at distances ˃ 10 meters between the camera and the target object; |
• Greater reliability compared to conventional methods; | • Unable to measure thickness and depth of any pathological manifestation. |
• Fast, non-invasive, non-destructive and contactless technology; | |
• Applicable at a considerable distance to analyze and inspect large areas at short intervals of time. |
Finally, one of the most critical factors when using aerial thermography is related to operation and equipment cost; however, when comparing benefits of this tool related to conventional methods, its potentialities considering its speed in data collection and safety for people performing an inspection are verified (Mavromatidis et al., 2014; Ariwoola, 2016).
3.2 Processing factors regarding thermal imaging
Thermographic analysis is a procedure where an inspector operates a thermal imager pointing at an object under inspection and detecting a defect by an analysis of thermogram obtained. Despite the technique is apparently simple, the result analysis might be complicated and would even lead to wrong conclusions if certain precautions are not taken before and during the test (Brique, 2016). Therefore, the operator himself must be aware of strong influence posed by solar radiation, wind and rain, and how these factors impact thermal distribution of any object analyzed in an open environment (Batista, 2019).
Considering this, in order to guarantee image quality, sensitivity and thermal contrast, awareness regarding some factors such as material emissivity (a function of surface temperature and observation angle) surface reflectivity, purpose of direct incident radiation and existing external sources (shadows, reflections), distance and measurement angle is required (Barreira, 2004; Cortizo, 2007; Bauer, 2015; Viégas, 2015; Batista, 2019). Besides, sun heat radiation may affect thermographic measurement, as it modifies normal heat flow from inside out. Distance from the equipment to the object may also modify surface temperature reading, as it reduces thermogram resolutions and influences atmospheric attenuation (Labat et al., 2011).
Regarding inspection time, it was found that differences between authors are present, but this parameter depends on environmental conditions found where a studied object is located (Rocha & Póvoas, 2017). In that sense, different behaviors were verified regarding measurement periods (dry and rainy), at 8 a.m., 3 and 9 p.m. (Freitas et al., 2014). In other cases, measurements were taken at different times during the morning and the afternoon (Nascimento, 2014), as emissivity by non-metal materials decreases with increasing temperature (Barreira, 2004). There were also cases where checking measurements throughout the day (6-18h), in order to evaluate the best measurement times, both in the morning and in the afternoon was decided (Viégas, 2015).
Finally, some authors (Uemoto, 2000; Watase et al., 2015; Hiasa et al., 2016) recommend an inspection at night in order to eliminate solar radiation effect, and have a better view between the defect and the intact regions , thus avoiding false detections (Rocha & Póvoas, 2017).
In addition, thermal gradients and turbulence modify air refractive index thus causing a reduction in image quality. Meanwhile, atmosphere present between the emission source and the receiver may cause disturbances in measurement. Therefore, a 10-meter distance between the emission source and the receiver must be maintained and measurements made at greater distances must be corrected (Barreira, 2004; Comitti, 2012; Viégas, 2015). Moreover, during days including winds above 7 m/s, measurements should not be made with infrared thermography, because data obtained will induce error in thermal analysis of the object (ITC, 2014).
According to Standard NBR 15572 (ABNT, 2013), an angle between the thermal imager and the inspected point must be as perpendicular as possible, so that no emissivity reduction due to inadequate observation angles (greater than 60º) is present. For this reason, Viégas (2015) states that nobody should remain directly facing the target so thermographer heat is not reflected. Therefore, positioning at an angulation of about 5º, in relation to object horizontal line to be thermally analyzed is recommended, as shown in Figure 6.
3.3 Flight Protocol
Project planning and development may vary according to fight capacity, being influenced by their accuracy and course (Agostinho, 2012). However, it is perceived that commercially available flight preparation tools, in some cases are still insufficient to perform certain inspections, and it is up to an operator to create their own tools and protocols (Seibert & Teizer, 2014). As a result, the protocol shown below in Figure 7 and Table 4, was developed according to studies by several authors (Agostinho, 2012; Siebert & Teizer, 2014; Ariwoola, 2016; Ellenberg et al., 2016; Entrop & Vasenv, 2017; Freimuth & König, 2018).
Table 4 Flight protocol
STEPS | PROCEDURES |
---|---|
1. Analysis of dynamic flight interactions | At this stage, checking UAV use regulations where inspection will be performed is required. Additionally, a study on weather conditions for inspection day, and characteristics of object studied (area, number of floors, maximum level) must be obtained and then proceed with choosing an equipment. |
2. Flight Area Description | On the second stage, performing a test flight to identify risk areas and establishing reading angles and distances is required. |
3. Flight Path Planning | Once risk areas have been determined, a flight path must be developed so that 75% of UAV load for flight autonomy is guaranteed. |
4. Inspection Performance | After completing previous steps, inspection may be performed in such a way that reading data safely and accurately is possible. |
By analyzing Table 4, it is verifiable that an initial stage is related to previous requirements for the inspection using a thermographic camera integrated with an UAV, including verifying any regulation for such equipment where the procedure will be performed, weather conditions, being necessary winds of less than 7 m/s and not during cloudy days, having knowledge of the object to be studied, such as dimensions and location, and finally choosing an equipment that guarantees a flight autonomy for such procedure. Afterwards, inspection area where the UAV will be moving along the inspection must be determined, paying attention to risk areas such as places where people, animals and obstacles are present, and establishing angles and distances where readings will be taken, at distances ˂ 10 meters and at angles according to Section 3.1, ensuring the accuracy of the data obtained. From there, a path to be traveled by the UAV must be planned in such a way that risk area displacement is avoided and the device has sufficient flying autonomy to finish a flight with 75% of charge in the battery, including energy consumed during landing and take-off procedures. Finally, once previous steps have been completed, the inspection may be performed.
3.4 Data Analysis provided by Literature
It was verified that despite simplicity in using a thermal imager to obtain thermograms during inspections, interferences and environmental conditions under which images were obtained should not be taken into account, thermogram analysis and interpretation might lead to erroneous conclusions (Takeda & Mazer, 2018). In addition, it was found that the larger and the more superficial a defect area is, the easier detection is (Rocha & Póvoas, 2017). In that sense, it was found that if R/d ratio (R: short defect dimension and d: defect depth from the surface) is greater than 1, defects are found; if this R/d ratio is equal to 0.45, they are detectable up to a depth of 10 centimeters (Farrag et al., 2016). Moreover, in thermal profiles presented in the thermograms for masonry a clear variation in surface temperature was present. This thermal difference denotes different materials present inside the masonry, due to quite distinct physical and chemical properties (Cortizo, 2007).
In addition, during inspection of a structure including ceramic coating it was verified that the best measurements were obtained after the facade was heated (passive technique), and that the thermogram in the afternoon had better clarity compared to morning thermogram (Viégas, 2015). Afterwards, when studying a building covered with mortar, it was found that the best times for measurement were from 11 a.m. to 12 p.m. and 5-6 p.m., and a "more vibrant" yellow coloration in the region including coating detachment was verified. In this region temperature increases unlike the rest of mortar-coated facade absent of pathological manifestations. Finally, when monitoring a structure covered with tile, the best times for measurement were between 9-10 a.m. and 2-3 p.m. (Viégas, 2015), thus confirming measurement times stated in 3.1.
A slight tendency in greater temperature differences (between areas with and without fissures) in the hottest areas, as well as greater dispersion of these variations measured in warmer areas were also observed (Freitas et al., 2014). Besides, at least a 5-meter distance between the UAV and the research objects to be safe was at first considered. While during the tests, this distance was increased to 10 meters, thus guaranteeing both reliable data obtained and aircraft safety (Entrop & Vasenev, 2017). Furthermore, simulation and flight model preparation comprises a more accurate inspection and better UAV performance, considering speed characteristics and battery recharge required (Freimuth & König, 2018).
4. Conclusions
Based on previous discussion and presented data, confirming thermography integrated with UAV is a capable tool to identify thermal anomalies associated to pathological manifestations is possible. Additionally, this mechanism optimizes building inspection process, enabling characterization of difficult-access areas without risking human safety. Besides, it provides fast and precise data which helps during inspection procedures and structure recovery tests.
However, few limitations are described fourfold: charging capacity is rather vulnerable, weather variations during flight, data obtained in the thermogram and object reflections in the surroundings may interfere in the results. Main contributions of this study include a specific flight protocol to use a thermographic camera integrated with a UAV and a review on principles and techniques involved in this procedure. The latter being a basis for future studies and research on development and expansion of monitoring models that tend to overcome disadvantages and guarantee effectiveness of this tool.