Introduction
The agricultural sector accounts for an estimated 20 % of global greenhouse gas (GHG) emissions (IPCC 2014). Mexico ranks 12th in relation to CO2 equivalent (CO2 eq) emissions with 374 million tons, of which 12.3 % comes from agricultural activities (SEMARNAT and INECC 2012). Nationally, the poultry industry accounts for 63 % of livestock production, but the national inventory of greenhouse gas emissions only reports CO2 emissions for manure management in the general agriculture category. Therefore, the carbon footprint for fossil energy use by the poultry activity is unknown (SEMARNAT and INECC 2013).
The Farm Energy Act (SAGARPA 2003) provides incentives in the energy rates for farm activities, in order to achieve greater productive effciency. However, poultry farms require energy to: provide adequate thermal comfort, ventilation, and lighting to birds; mobilize feed, equipment, inputs and waste; dispose of mortalities and obtain water (Costantino et al. 2016). To determine the environmental impact of the energy consumption resulting from poultry farming, the matter and energy inputs and outputs from the chicken meat production process should be established and the CO2 emissions generated should be estimated. Therefore, the objective was to define the energy demand (MJ) to produce one kilogram of chicken meat and to determine the associated CO2 eq emissions.
Materials and Methods
Location of the study area
The study was conducted in the summer of 2013 in a farm located in the municipality of Taretan, in the western region of the State of Michoacán, Mexico, located at 19° 20' 00'' NL and 101° 55' 00'' WL. The climate is temperate with summer rains, average annual rainfall of 1 560 mm and temperatures between 4.4 and 29.6 °C. The farm has 10 poultry houses of 13 x 150 m, with capacity for 22 000 birds per 49-day cycle. The production system is technified, with a controlled environment composed of heaters, fans, extractors, sprinklers for moisture control and a curtain system on the house walls.
Determination of energy consumption
A survey conducted to learn the farm's overall process was applied to the poultry house keepers and the farm manager. The objective of the survey was to determine: the inputs and outputs of the process; the cycle's duration; consumption of LP gas (kg), electricity (kWh), feed (kg) and water (L); number of birds and live and carcass weight (kg) at the end of the production cycle. An inventory of machinery and equipment was carried out to determine the energy demand and hours of use. Fuel consumption in machinery and transportation vehicles was obtained from the farm's usage log.
The considerations for the calculations were that the basis of the report was for 1 000 birds during a 49-d production cycle; 13-hour d-1 operation of the ventilation and air extraction systems; the use of heating and lighting was for 28 d during the 49-d production cycle; 1.7 kg carcass weight without head, neck, legs and viscera; and live weight of 2.54 kg at the end of the 49-d production cycle.
Analysis of energy performance
It was determined with the energy productivity and specific energy equations of Singh (1997) and Salazar et al. (2012), which are as follows:
Where EP = Energy productivity.
Where SE = Specific energy.
Determination of GHG emissions by energy consumption
GHG emissions from electric energy consumption to provide drinking water, feed, lighting, ventilation and air extraction were estimated based on the CO2 eq emission factor for Mexico of 454 g CO2 eq per kWh proposed by the International Energy Agency (IEA 2015). The National Institute of Ecology's carbon calculator (INECC and SEMARNAT 2013) was used to determine the GHG emissions of the LP gas-based heating system, while the determination of the electric energy consumption (kWh) used to extract and distribute drinking water (m3) was performed with the Michoacán efficiency index, which is 0.75 kWh m-3 (CONUEE 2011).
Results and discussion
The main system inputs and outputs for a broiler production cycle are described in Figure 1. The consumption of feed, water and electricity has variations throughout the production cycle, according to the age of the bird. The energy demand for the Taretan farm is summarized in Table 1; for 1 000 broilers the demand is 22 834 MJ. Therefore, the estimated energy productivity for broiler live weight is 0.12 kg MJ-1, while the specific energy demanded is 9.2 MJ kg-1. About 98 % of the energy consumption is due to the heating system, even though LP gas is required in only four weeks of the production cycle. This coincides with the figure reported by Sonesson et al. (2009), who indicate that fuel consumption for heating accounts for between 80 and 90 % of the total energy used, which suggests an area of opportunity in which strategies that reduce energy consumption should be focused on. On the other hand, an FAO study (2013) found that the energy consumption was 4.5 MJ kg-1 carcass weight, which is lower than that found in the present study, which may be due to the fact that this study took into account the energy consumed by the ventilation and heating systems. In addition, the energy productivity for broiler live weight of 0.12 kg MJ-1 is higher than that obtained in a simulation carried out by Sefat et al. (2014), where they obtained an energy productivity of 0.01 kg MJ-1, in which the energy contributions for feed production and manure management were considered. In comparing the specific energy required for the production of chicken meat (Lammersa et al. 2010) and beef (Sonesson et al. 2009), they were found to have similar values (Table 2), but they come from different inputs, such as consumption of LP gas for heating chickens and the consumption of diesel for the machinery required for beef production.
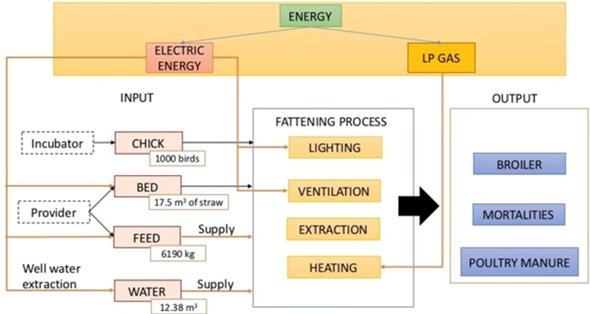
Figure 1. Main inputs for the production of 1 000 broilers on a farm in the Municipality of Taretan in a 49-d production cycle.
Table 1. Supply of inputs and energy demanded for the production of 1 000 broilers at a farm in the Municipality of Taretan in a 49 d production cycle.

The energy demand translates into 1 206.4 kg CO2 eq (Table 1). That is, 0.47 kg CO2 eq are generated per kilogram of broiler live weight or 0.70 kg CO2 eq to produce a kilogram of carcass meat. The farm's CO2 eq emissions (Table 3) were lower than those of other poultry systems (Thynelius 2008, Williams et al. 2006, Wiedemann et al. 2017) and those reported for the production of pork and beef (Roy et al. 2011, Cederberg et al. 2009). However, it is necessary to take into account the following considerations when comparing CO2 eq emissions between livestock production systems: 1) differences in production systems evaluated, climatic conditions and management practices of each farm; 2) the limits of research in each report vary, and 3) some results were calculated on the basis of estimates made in other countries, such as that of Roy et al. (2011) made for meat production in Japan and that of Cederberg et al. (2009) in Sweden.
Table 3. CO2 eq emissions from different chicken meat production processes.

◊ Live weight, ∆ Broiler carcass weight, ‡ C Frozen Chicken Meat .
The present study focuses on the energy consumption inside the poultry house, but does not consider the production of poultry feed, a process reported as the largest energy consumer (Nguyen et al. 2012, Wiedemann et al. 2017). The energy used during the production of poultry feed was calculated by Nguyen et al. (2012); if this value is added to the figure already obtained, the estimated GHG emissions per kilogram of broiler live weight increases to 61.9 kgCO2 eq. According to Pelletier (2008), feed provision accounts for approximately 80 % of the energy consumed and 82 % of greenhouse gas emissions.
There are no national estimates for GHG emissions from poultry farming in Mexico. However, if the farm studied is considered to be typical in this country, the results suggest that the GHG contribution by poultry farms would increase the emissions reported for the agriculture subcategory by 13 % (SEMARNAT and INECC 2013) (Figure 2).

Figure 2. Estimation of the contribution of poultry farming to GHG emissions in Mexico: Agriculture Subcategory.
Energy demand for the production of one kilogram of chicken meat and the associated CO2 eq emissions were determined; this information can serve as a starting point to know the average actual energy consumption of the poultry industry in Mexico and to find areas of opportunity to reduce GHG emissions. The next step should be to determine the energy demand of the entire supply chain to know the total energy consumption for the production of chicken meat and its derivatives.